Introduzione
L’imballaggio: ruoli e funzioni di un oggetto complesso
Nel panorama contemporaneo, l’imballaggio ha acquisito una rilevanza sempre maggiore: è un elemento essenziale che consente ai prodotti di accedere al circuito delle merci. È un oggetto complesso, caratterizzato da molteplici funzioni: oltre a essere un mezzo pratico per proteggere e contenere i beni di consumo, il packaging è riconosciuto come un importante punto di contatto tra le aziende e i consumatori, rappresentando un potente strumento di comunicazione per trasmettere le qualità del prodotto e i valori della marca.
Da un punto di vista normativo, l’articolo 218 del Decreto Legislativo 152 del 2006, al comma 1a, definisce l'imballaggio come un “prodotto, composto di materiali di qualsiasi natura, adibito a contenere determinate merci, dalle materie prime ai prodotti finiti, a proteggerle, a consentire la loro manipolazione e la loro consegna dal produttore al consumatore o all'utilizzatore, ad assicurare la loro presentazione, nonché gli articoli a perdere usati allo stesso scopo”. Nello stesso articolo, al comma 1b, vengono poi catalogati gli imballaggi in tre categorie:
- l’imballaggio per la vendita o imballaggio primario, “concepito in modo da costituire, nel punto di vendita, un’unità di vendita per l'utente finale o per il consumatore”;
- l’imballaggio multiplo o imballaggio secondario, “concepito in modo da costituire, nel punto di vendita, il raggruppamento di un certo numero di unità di vendita, indipendentemente dal fatto che sia venduto come tale all'utente finale o al consumatore, o che serva soltanto a facilitare il rifornimento degli scaffali nel punto di vendita. Esso può essere rimosso dal prodotto senza alterarne le caratteristiche”;
- l’imballaggio per il trasporto o imballaggio terziario, “concepito in modo da facilitare la manipolazione ed il trasporto di merci, dalle materie prime ai prodotti finiti, di un certo numero di unità di vendita oppure di imballaggi multipli per evitare la loro manipolazione ed i danni connessi al trasporto, esclusi i container per i trasporti stradali, ferroviari marittimi ed aerei”.
Tra le numerose funzioni che deve assolvere, il packaging deve dunque garantire l'adeguato contenimento del prodotto per cui è stato progettato. Questa funzione fondamentale implica la creazione di uno spazio sicuro e adatto per il bene destinato al consumatore, in modo che possa essere maneggiato e trasportato senza rischi di danneggiamento o contaminazione. Altresì, l’imballaggio deve fornire una robusta protezione al proprio contenuto da fattori esterni. Questi includono sia aggressioni fisiche, come urti e contatti accidentali con altri oggetti, sia agenti chimici come acqua, umidità e aria che potrebbero compromettere le qualità del prodotto, la sua integrità e la sua durabilità. La sua capacità di resistere a tali minacce esterne è cruciale per preservare il contenuto nel corso del tempo e lungo il suo intero ciclo di vita. Infine, il packaging deve facilitare il trasporto e agevolare la manipolazione del prodotto, dalla fase di produzione, lungo l'intera catena di distribuzione, fino al punto vendita e al contesto di utilizzo e consumo. L’efficienza logistica contribuisce a ridurre i costi operativi e a garantire che il bene per cui è stato progettato arrivi in perfette condizioni nelle mani del consumatore.
Oltre alla sua natura di oggetto d’uso, il packaging si presenta poi come un potente mezzo di comunicazione, che veicola informazioni rilevanti sul prodotto e ne trasmette il valore ai consumatori. È un “dispositivo comunicativo”, che costituisce una forma di mediazione tra la filiera produttiva e gli utenti finali. Attraverso gli elementi grafici, le forme e i suoi materiali, il packaging trasmette gli attributi distintivi del contenuto, così come del contenitore. Fornisce avvertenze e informazioni essenziali sul prodotto, come, per esempio, la sua scadenza o la sua composizione (D.Lgs. 116/2020); inoltre, offre indicazioni utili rispetto alle istruzioni per l'uso e alla gestione del fine vita, costituendo una vera e propria interfaccia per l’interazione. In questo modo, l’imballaggio costituisce non solo un elemento chiave per il sistema marca, ma uno strumento essenziale al servizio del consumatore.
Le origini degli imballaggi risalgono agli albori della civiltà: le prime forme di proto-imballaggi erano costituite da materiali naturali come zucche, conchiglie e fogliame, nonché da tronchi scavati e organi di animali. Successivamente, con l’introduzione della lavorazione dei metalli e della ceramica, furono sviluppate anfore e altre forme, in alcuni casi ancora presenti nella società odierna. La storia dell’imballaggio è strettamente legata ai cambiamenti socioculturali e delle abitudini di consumo. Per questo, nel tempo, il packaging si è evoluto considerevolmente proprio per adattarsi alle esigenze in continua mutazione della società e dell'ambiente. Grazie all’innovazione tecnologica, si sono affermati i cosiddetti imballaggi funzionali, attivi o intelligenti. Tali confezioni sono caratterizzate dall’aggiunta di elementi tecnologicamente avanzati che potenziano la conservazione del prodotto, lo scambio di informazioni lungo la filiera e l’esperienza di consumo per l'utente finale.
In queste linee guida si analizzano, in particolare, gli imballaggi in acciaio a uso domestico e industriale, nonché il ruolo del packaging design nel facilitare il riciclaggio e più in generale le azioni di prevenzione a essi associati,anche nell’ottica di perseguire gli obiettivi di sostenibilità e circolarità che negli ultimi anni sono diventati sempre più prioritari nel contesto comunitario.
Prevenzione e riciclo: progettare gli imballaggi in chiave di circolarità
La normativa di riferimento per la gestione dei rifiuti di imballaggio è la Direttiva 94/62/CE, la quale è oggetto di continui aggiornamenti. Tale Direttiva istituisce le basi normative per la gestione degli imballaggi nell'Unione Europea. In particolare, pone l'accento sulla prevenzione della produzione di rifiuti di imballaggio attraverso la promozione di soluzioni di imballaggio leggere e la promozione del riciclaggio. Stabilisce una gerarchia preferenziale nella gestione dei rifiuti, con l'obiettivo principale di prevenirne la generazione, mediante il riuso e il riciclo, incoraggiando la progettazione di imballaggi che riducano al minimo il volume e il peso necessario per garantire la sicurezza, l'igiene e l'accettabilità del prodotto, nell’ottica di preservare le risorse e minimizzare il carico ambientale.
Tra gli aggiornamenti più recenti, la Direttiva (UE) 2018/852 - nota come "Direttiva sui rifiuti di imballaggio" - rafforza ulteriormente gli obiettivi di gestione sostenibile degli imballaggi e dei rifiuti generati da essi. Tra le modifiche più significative si evidenziano obiettivi di riciclaggio più ambiziosi, una maggiore enfasi sulla prevenzione degli sprechi attraverso la progettazione degli imballaggi e una più marcata enfasi sulla responsabilità estesa del produttore. Quest'ultima implica che i produttori devono essere coinvolti in maniera più attiva nell'intero ciclo di vita dei loro prodotti, includendo il loro smaltimento responsabile. In aggiunta, la direttiva sostiene l'implementazione di sistemi di restituzione e/o raccolta degli imballaggi usati e dei rifiuti di imballaggio, coinvolgendo attivamente produttori e consumatori. In tal modo, si promuove una logica circolare che considera il ciclo di vita completo del prodotto, garantendo una gestione responsabile e sostenibile dei materiali d'imballaggio.
Nell’ultimo decennio, l'Unione Europea sta, infatti, attivamente promuovendo, oltre al concetto di sostenibilità, anche quello di economia circolare, puntando sulla riduzione degli sprechi e il riutilizzo delle risorse per mitigare gli impatti di produzione e consumo sull’ambiente. Un passo significativo in questa direzione è rappresentato dal “Piano d'Azione per l'Economia Circolare”, adottato nel dicembre 2015. Questo piano è diventato uno dei pilastri fondamentali del cosiddetto “Green Deal” europeo, un ambizioso programma volto a rendere l'Europa più sostenibile dal punto di vista ambientale, economico e sociale.
Il Piano d'Azione per l'Economia Circolare mira a promuovere i principi della circolarità e ad aumentare la consapevolezza tra produttori e consumatori. Le sue 54 azioni concrete includono l'etichettatura, il miglioramento dell'efficienza dei materiali, la promozione dell'alta riparabilità dei prodotti, oltre alla gestione responsabile dei prodotti al termine del loro ciclo di vita. Un elemento chiave di questo approccio è l'attenzione alla progettazione dei prodotti in modo che siano durevoli, affidabili, riutilizzabili, riparabili ed efficienti dal punto di vista energetico. Tali accorgimenti, non solo contribuiscono a ridurre i rifiuti, ma anche a raggiungere gli obiettivi climatici del Green Deal.
Al fine di applicare queste strategie di progettazione al settore degli imballaggi e sviluppare contenitori in modo circolare, è possibile adottare due approcci alla prevenzione e alla promozione del riciclaggio: da una parte, si possono utilizzare, in modo parziale o totale, materiali già riciclati; dall’altra, considerare la riciclabilità di un packaging sin dalla sua ideazione, anticipando come l’oggetto verrà smaltito e riciclato al termine del suo ciclo di vita e progettandone di conseguenza le sue caratteristiche, per esempio in termini di separabilità dei componenti, di eliminazione di elementi non riciclabili, di colle o materiali tossici, ecc. Il primo approccio viene chiamato “Design from Recycling”, cioè progettazione a partire dal riciclaggio, mentre il secondo “Design for Recycling”, cioè progettazione per favorire il riciclaggio.
Se il Design from Recycling sottolinea l'importanza di utilizzare materiali già esistenti che sono stati recuperati e riciclati, coinvolgendo la raccolta e il riciclaggio dei rifiuti, in modo da ridurre la necessità di estrazione e produzione di materie prime vergini, il Design for Recycling presuppone che la riciclabilità di un imballaggio debba essere un requisito obbligatorio fin dalla fase iniziale del suo sviluppo, oltre a ripensare l’oggetto o parti di esso, in modo da prolungarne la vita utile, promuovendone per esempio il riuso. In questo senso, è fondamentale la partecipazione al processo di progettazione di designer, ingegneri, produttori e consumatori.
Passare da un approccio lineare a uno circolare, che considera il ciclo di vita complessivo di un oggetto, è fondamentale per la creazione di packaging circolari. L’obiettivo è quello di garantire che l’imballaggio abbia una nascita e, idealmente, una continua rinascita - secondo una visione detta “from cradle to cradle” -, allontanando il più possibile nel tempo il momento in cui si trasformerà in rifiuto. La progettazione dei packaging, oltre a concentrarsi sull'oggetto in sé e sui processi di produzione e trasformazione, dovrebbe quindi mantenere una visione più ampia e sistemica e incorporare, fin dall'inizio del processo, un’anticipazione di come l'imballaggio e le sue diverse parti saranno riutilizzate o riciclate.
Imballaggi in acciaio: favorire il riciclo attraverso la progettazione
L'obiettivo di tale documento è quello di fornire indicazioni progettuali utili ai progettisti e alle aziende coinvolte nella produzione e nell'utilizzo di packaging in acciaio, al fine di facilitarne il processo di riciclo.
Le seguenti linee guida rientrano nelle strategie di prevenzione promosse da CONAI all’interno del progetto “Pensare Futuro”, che racchiude una serie di strumenti di eco-progettazione degli imballaggi messi a disposizione alle imprese.
Le iniziative atte a facilitare le attività di riciclo degli imballaggi si configurano come una delle sette leve di prevenzione promosse dal Consorzio. Le leve di prevenzione sono intese come criteri utili alla ricerca, progettazione e valutazione di soluzioni che possano portare a prevenire l’impatto ambientale degli imballaggi nel loro ciclo di vita, ovvero:
- il risparmio di materia prima;
- il riutilizzo;
- l’utilizzo di materiale riciclato;
- l’ottimizzazione della logistica;
- la facilitazione delle attività di riciclo (sulla quale si concentra l’attenzione del presente documento);
- la semplificazione del sistema di imballo;
- l’ottimizzazione dei processi produttivi.
L'approccio adottato è quello di fornire linee guida e checklist per sostenere progettisti e aziende nel processo decisionale, considerando la complessità e la varietà degli imballaggi quanto a struttura, composizione e prestazioni, nonché le differenze nella gestione della fine della loro prima vita utile che ad esse conseguono. È utile, quindi, in fase progettuale, assicurare un effettivo miglioramento delle performance ambientali in tema di riciclabilità; è essenziale il confronto con gli attori della filiera di riferimento e la verifica dei risultati ottenuti lungo tutto il ciclo di vita dal binomio imballaggio-prodotto, con il supporto di esperti del settore. Il tema della riciclabilità degli imballaggi richiede, inoltre, di tenere sempre in considerazione le possibilità reali offerte dalle attuali tecnologie di selezione e riciclo installate a livello industriale in una determinata realtà geografica. Le indicazioni fornite saranno, dunque, periodicamente aggiornate da CONAI. Conoscere i processi e le loro specificità aiuta a comprendere le conseguenze delle scelte progettuali che influenzano fasi importanti dell’operazione di riciclo, individuando le alternative più adatte per ottimizzare il processo.
La pubblicazione è divisa in otto capitoli, sviluppati a partire da un’introduzione generale sull’imballaggio, per convergere nella descrizione del processo di produzione dell’acciaio, i principali semilavorati e tipologie di imballaggi in acciaio fino ad arrivare al suo processo di raccolta e riciclo, così da rendere chiare le motivazioni alla base delle indicazioni progettuali proposte nel capitolo conclusivo. La struttura è stata così pensata per rispondere alle esigenze di progettisti e aziende, evidenziando i punti di attenzione che hanno portato alle indicazioni progettuali proposte.
Nella prima parte del documento, dopo l'introduzione vengono descritte le caratteristiche dell’acciaio e i processi di produzione primaria e secondaria del materiale, i semilavorati per la produzione di imballaggi in acciaio e le principali tipologie di imballaggio.
Nella seconda parte vengono, invece, descritti i processi di raccolta, selezione e riciclo degli imballaggi in acciaio, soffermandosi sulle principali modalità della filiera e approfondendo i vari trattamenti utilizzati durante l’intero processo.
La terza e la quarta parte presentano le linee guida utili per la facilitazione delle attività di riciclo degli imballaggi in acciaio destinati all'uso domestico e conferiti nella raccolta differenziata urbana.
Queste linee guida offrono a progettisti e tecnici una checklist pensata per essere utilizzata sia in fase di produzione che di sviluppo dell’imballaggio, sia come strumento di possibile valutazione per identificare margini di miglioramento. A tal proposito, le linee guida qui presentate hanno l’obiettivo di evidenziare problemi e possibilità di soluzione, ma non hanno la pretesa di essere esaustive e di trattare in modo differenziato tutte le situazioni riscontrabili. Per questo motivo, sono riportati in fondo al documento tutti i riferimenti delle fonti consultate per la stesura e le indicazioni normative utili per approfondire quanto trattato nei diversi capitoli. Inoltre, le linee guida redatte sono riferite al panorama italiano; quindi, è necessario considerare che alcune specificità della filiera possono differire per la loro natura organizzativa o tecnologica rispetto agli altri Paesi della Comunità Europea.
Gli imballaggi in acciaio
Aspetti introduttivi
I packaging in acciaio presentano numerosi vantaggi in termini di proprietà intrinseche e di riciclabilità. Una delle loro caratteristiche principali è rappresentata, analogamente ad altri contenitori in metallo, dalla possibilità di riciclare il materiale in modo potenzialmente infinito, in quanto è possibile reintrodurre la materia prima seconda all'interno di nuovi cicli produttivi, garantendo alti livelli di qualità e proprietà analoghe a quelle dell'acciaio vergine, anche dopo innumerevoli cicli di recupero.
In generale, l'acciaio ottenuto dal riciclo è destinato a settori produttivi diversi da quello degli imballaggi, poiché questi ultimi, soprattutto se destinati a contenere alimenti, devono soddisfare standard e requisiti tecnici specifici che portano, nella scelta della materia prima, a privilegiare l'acciaio vergine; nonostante ciò, privilegiare dove possibile l’uso di materiale riciclato riduce il consumo di risorse, rispetto alla produzione di materie prime vergini, con benefici ambientali significativi. È per questo che l’associazione di categoria ANFIMA promuove tra i produttori di imballaggi in acciaio e i loro clienti l’utilizzo del marchio “Metal Recycles Forever”, ideato dall’associazione Metal Packaging Europe (MPE). Inoltre, la possibilità di rigenerare alcuni imballaggi esistenti e renderli riutilizzabili limita la necessità di produrre nuovi contenitori e il relativo consumo di risorse.

Mediante una gestione efficiente delle risorse, in termini sia di materia che di energia, insieme a un’opportuna progettazione, l’uso dei packaging in acciaio può dunque contribuire fattivamente a ridurre l'impatto ambientale del settore dell’imballaggio e sostenere la transizione verso processi sempre più circolari.
Se osserviamo il panorama italiano, gli imballaggi in acciaio rappresentano circa il 2% della produzione siderurgica. Nel corso del 2022, nel nostro Paese sono stati prodotti circa 21 milioni di tonnellate di acciaio, posizionandosi come secondo produttore dell'Unione Europea dopo la Germania. Rispetto a tale produzione, sono stati immessi sul mercato oltre 500.000 tonnellate di packaging in acciaio, evidenziando il loro ampio impiego nel confezionamento di una vasta gamma di prodotti. La raccolta post-consumo di tali imballaggi ha raggiunto risultati notevoli: oltre l'80% dei quantitativi immessi a consumo, pari a circa 420.000 tonnellate, è stato avviato al processo di riciclo. Questi dati testimoniano l'efficacia del sistema di raccolta e riciclo nella filiera dell’acciaio.
Acciaio: caratteristiche e proprietà
L'acciaio è un materiale altamente versatile: oltre che per gli imballaggi di uso domestico e industriale, viene impiegato in diversi settori, come l’edilizia, l’industria automobilistica e dei trasporti, la produzione di utensili e macchinari; inoltre, è impiegato nella realizzazione di supporti per pannelli solari, turbine eoliche, dighe e veicoli elettrici, elementi di fondamentale importanza per la transizione energetica.
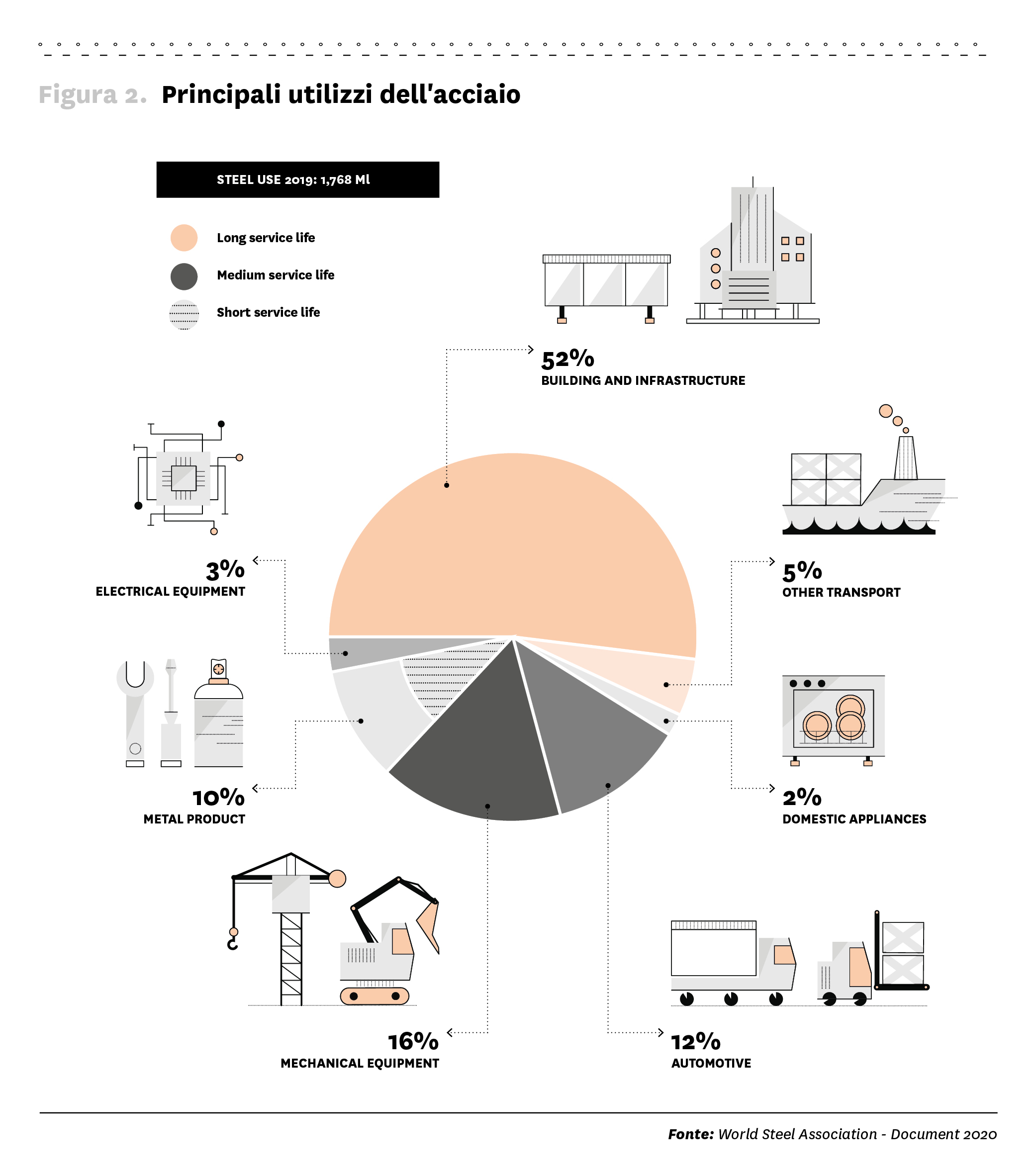
Grazie alla sua elevata resistenza alla corrosione, l'acciaio è ideale per i manufatti esposti agli agenti atmosferici e alle condizioni ambientali avverse. La sua elevata resistenza alla trazione e all'usura, inoltre, lo rendono adatto anche per applicazioni soggette ad alta pressione e sollecitazioni meccaniche.Modificando la sua composizione, è possibile ottenere caratteristiche diverse, declinabili per le specifiche applicazioni. L'acciaio è, infatti, una lega metallica complessa costituita principalmente da ferro e carbonio, le cui proprietà fisiche e meccaniche variano in base alla presenza di altri elementi.
La quantità di carbonio presente nella lega varia generalmente tra 0,2% a 2%, tuttavia, se presente in quantità maggiori, l'acciaio assume un comportamento meccanico differente, tipicamente più fragile e classificato come ghisa. La composizione dell'acciaio può essere modificata aggiungendo altri elementi di lega come boro, cromo, manganese, molibdeno, nichel, niobio, titanio o vanadio. Questi elementi influenzano specificamente le proprietà dell’acciaio: ad esempio, ne migliorano la resistenza alla corrosione (mediante l’aggiunta di nichel e titanio) o la resistenza alla trazione (aggiungendo molibdeno e cromo). Altri elementi come nichel, manganese e cromo possono contribuire a migliorare le performance di tenacità e durezza. Inoltre, le proprietà dell'acciaio possono essere modificate anche attraverso i processi produttivi e il trattamento termico come la laminazione e il temperaggio, che consentono di ottimizzarne, per esempio, lo snervamento, la duttilità e la rigidezza.
Grazie alla sua versatilità, l'acciaio può essere facilmente lavorato in diverse forme e dimensioni per soddisfare svariate esigenze, rendendolo una scelta flessibile e conveniente anche per l'industria degli imballaggi. In questo ambito si utilizzano, in particolare, i cosiddetti acciai dolci, che presentano un basso tenore di carbonio e un’alta processabilità. L’efficacia del materiale nel proteggere i prodotti da urti e danni durante il trasporto, resistendo a sollecitazioni meccaniche, graffi e abrasione, lo rende ancora oggi una scelta popolare per l'industria. Inoltre, l'acciaio offre un'efficace barriera contro gli agenti esterni, riducendo il rischio di ossidazione e degradazione del prodotto confezionato. Queste peculiarità lo rendono ideale per il confezionamento di prodotti chimici e farmaceutici, dove è necessaria una barriera contro agenti aggressivi come acidi o sostanze caustiche. L'acciaio viene anche utilizzato nel settore alimentare e delle bevande, per cui vengono solitamente impiegate leghe quali acciai inossidabili e acciai rivestiti di ossidi come cromo e stagno; in alcuni casi, vengono utilizzate leghe ad alto tenore di carbonio (ghise) e leghe contenenti rame.
La produzione dell’acciaio
Nel corso del 2022 la produzione globale di acciaio ha raggiunto la quota di 1,9 miliardi di tonnellate, evidenziando il ruolo significativo di questo materiale nel panorama industriale contemporaneo; come già anticipato, l'acciaio è di fondamentale importanza in diversi settori industriali, con una particolare concentrazione nell'edilizia e nelle infrastrutture.
Approssimativamente, sempre a livello mondiale, il processo di produzione di acciaio vede il 70% del suo grezzo ottenuto tramite altoforno (produzione primaria), utilizzando il minerale di ferro come materia prima vergine; il rimanente 30% deriva invece da processi ad arco elettrico, impiegando il rottame ferroso come materia prima seconda (produzione secondaria).
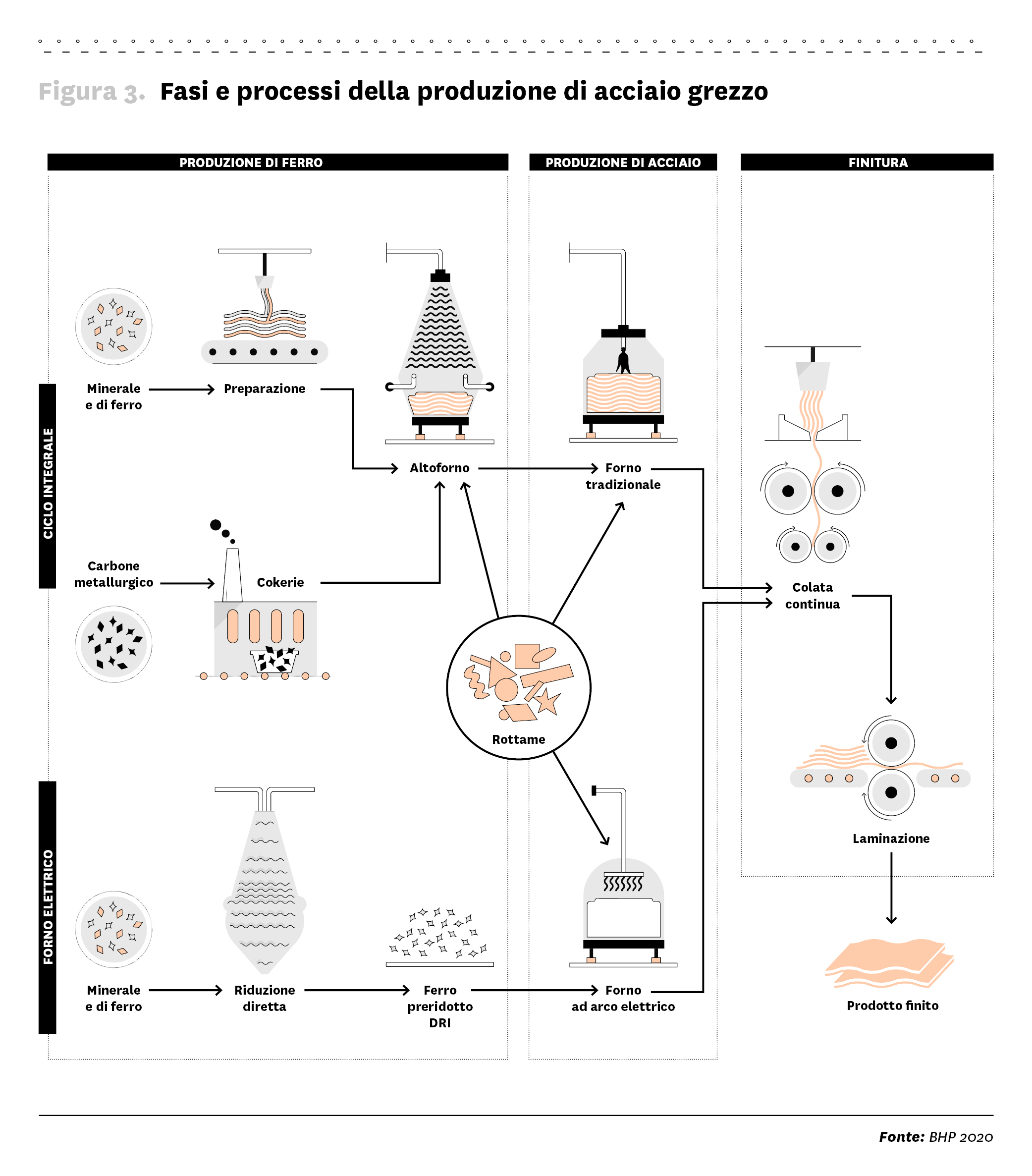
Produzione da altoforno
L’altoforno rappresenta la tecnologia più antica e attualmente più diffusa per la produzione di ghisa e acciaio a partire da minerali ferrosi, ma è anche la più energivora. Nell'altoforno, infatti, avviene una complessa reazione di riduzione del ferro a temperature estremamente elevate, oltre i 1500 °C.
Il processo dell'altoforno si basa sull'utilizzo di minerali di ferro, il coke (ottenuto da carboni fossili) e il calcare. Il coke è il risultato di un processo di distillazione a cui sono sottoposti i carboni fossili prima di essere impiegati nell'altoforno; è particolarmente resistente al calore ed è essenziale per la trasformazione del minerale di ferro in ghisa.
Il coke, insieme ai minerali di ferro e ad altre sostanze, viene introdotto nell'altoforno per produrre la ghisa liquida, che costituisce il prodotto intermedio per la produzione dell'acciaio. Una volta ottenuta la ghisa liquida, essa viene trasferita all'acciaieria tramite carri ferroviari appositamente progettati, noti come “carri siluro”.
Per ottenere l'acciaio, la ghisa deve poi subire un'operazione di depurazione del carbonio. Questo avviene attraverso l'utilizzo di grandi convertitori, all'interno dei quali viene versata la ghisa liquida e, mediante insufflaggio di ossigeno, viene ridotto il contenuto di carbonio.
L'acciaio liquido risultante viene quindi trasferito agli impianti di colata continua, dove viene versato in apposite lingottiere per avviare il processo di solidificazione. È durante questo processo che l'acciaio si raffredda e solidifica, dando luogo alla formazione di semilavorati noti come bramme. Queste ultime sono successivamente trasformate in laminati a caldo, che vengono poi utilizzati in diverse applicazioni industriali.
Produzione da forno elettrico
Oltre all’altoforno, vengono utilizzati per la produzione di ghisa e acciaio anche i forni elettrici ad arco. L’uso di questo tipo di forni caratterizza in particolare il settore siderurgico italiano, caratterizzato da numerose piccole e medie imprese localizzate in prossimità dei centri di consumo dell'acciaio.
Il processo di produzione si basa principalmente sull'impiego di rottami ferrosi, cioè materie prime secondarie, riducendo l'utilizzo di materie prime vergini, che implica un maggiore impatto in termini di consumo di risorse e di emissioni. I rottami ferrosi utilizzati nel processo provengono generalmente da attività di demolizione di strutture industriali, civili e navali, dal disassemblaggio di autovetture ed elettrodomestici, da scarti di lavorazione, dalla raccolta di imballaggi e altri rifiuti domestici.
All’inizio del processo di produzione i rottami vengono selezionati e bonificati per garantire una adeguata qualità del materiale in entrata. Successivamente, vengono fusi all’interno del forno elettrico: il materiale viene caricato nel forno, portato alla temperatura di fusione e poi sottoposto a estrazione delle scorie di produzione che affiorano in superficie.
Durante la fusione, che avviene in maniera continua, i rottami sono combinati con elementi di lega per ottenere la composizione desiderata dell'acciaio. L'acciaio fuso viene poi estratto e sottoposto a ulteriori fasi di lavorazione, durante le quali possono essere aggiunti altri elementi per migliorarne ulteriormente le caratteristiche.
Alla fine del processo, mediante estrusione, si ottengono i semilavorati, spesso sotto forma di billette. Tali semilavorati rappresentano la base per una ampia varietà di applicazioni industriali, e contribuiscono a dare nuova vita ai rottami post-consumo e a ridurre l'impatto ambientale del processo produttivo dell'acciaio.
Impatti ambientali della produzione dell’acciaio
La produzione di acciaio comporta impatti ambientali significativi in diverse fasi del processo, dalla fase di estrazione e lavorazione iniziale, fino alla produzione vera e propria. Richiede notevoli quantità di energia e genera emissioni che incidono sul clima, sulla qualità dell’aria, sulle condizioni del suolo e delle falde acquifere. Basti pensare che, a livello globale, gli 1,95 miliardi di tonnellate di acciaio prodotti nel 2021 hanno generato circa 3,7 miliardi di tonnellate di CO₂, pari a circa il 10% delle emissioni dovute al consumo di combustibili fossili.
La maggior parte di queste emissioni, circa il 92%, è tuttavia da imputarsi alla produzione primaria, prevalentemente da processi a ciclo integrale con altoforno e convertitore, che corrisponde approssimativamente al 75% della produzione mondiale; solo l’8% riguarda invece la produzione secondaria in impianti con forno ad arco elettrico alimentato con rottame di ferro, circa il 25% della produzione mondiale.
Nella produzione primaria, infatti, le emissioni specifiche di produzione sono mediamente pari a 2,2 tonnellate di CO₂ per ogni tonnellata di acciaio grezzo prodotto: un valore nettamente superiore a quelle della produzione secondaria, che si attesta tra le 0,1 e le 0,7 tonnellate di CO₂ per tonnellata di acciaio, a seconda della quota di energia da fonti rinnovabili nel mix di produzione di energia elettrica utilizzato dagli impianti.
Secondo una recente stima (Wang P. et al., 2021), grazie ai miglioramenti tecnologici nella produzione primaria e alla crescita di quella secondaria, nell’ultimo secolo le emissioni di CO₂ per tonnellata di acciaio si sono ridotte di circa il 70%.Nel corso del tempo, l’industria dell’acciaio ha sensibilmente ridotto le emissioni specifiche di produzione, per quanto la crescita esponenziale della produzione globale ne abbia sostanzialmente compensato gli effetti positivi in termini di impatto sul clima.
Materiali per imballaggi in acciaio
Dalla produzione dell'acciaio si possono ottenere diversi tipi di semilavorati. I laminati lunghi comprendono travi, vergelle e tondini per il cemento armato. I laminati piani sono costituiti da nastri d’acciaio, solitamente stoccati sotto forma di coil, avvolti cioè in rotoli; questo tipo di laminati comprende, per esempio, la banda stagnata o cromata e altri lamierini da imballaggio.
Banda stagnata
La banda stagnata è costituita da un lamierino d’acciaio dolce, rivestito su entrambi i lati da uno strato uniforme e sottile di stagno dallo spessore di pochi centesimi di millimetro.
Il processo di stagnatura avviene a ciclo continuo: il nastro di acciaio viene fatto passare in una serie di vasche che contengono acido di solfato di stagno e, mediante elettrolisi e successivi altri processi chimici, viene ricoperto da un film di ossido di stagno. Gli acciai che devono essere posti a contatto con gli alimenti vengono ulteriormente trattati e sottoposti a laccatura.
Grazie alle sue proprietà, la banda stagnata è uno dei semilavorati più utilizzati per la produzione di imballaggi. È impiegata specialmente in ambito alimentare, poiché soddisfa i requisiti igienico-sanitari richiesti dal settore. La stagnatura, infatti, impedisce l’ossidazione dell’acciaio e lo rende, quindi, particolarmente resistente agli acidi (per esempio, nel caso di conserve a base di frutta o pomodoro).
La banda stagnata è apprezzata, inoltre, per la sua versatilità in termini di stampa o incollatura. Infine, è facilmente saldabile e si presta a essere modellata e tagliata con facilità.
Dal punto di vista del riciclaggio, lo stagno potrebbe costituire un elemento pregiudizievole nei processi di fusione effettuati dalle acciaierie, per questo sarebbe opportuno prevedere una sua separazione dalla frazione ferrosa mediante un processo di distagnatura. Oltre al recupero dello stagno, tale procedimento permette anche di ottenere come beneficio indotto un rottame di ferro di maggiore qualità.
Questo processo di lavorazione comporta dei costi nettamente superiori al classico sistema frantumazione; per questo motivo, nella stragrande maggioranza la banda stagnata viene conferita direttamente alle acciaierie e fusa insieme agli altri rottami di ferro. Tuttavia, ciò non incide sul processo di riciclaggio, poiché la banda stagnata, rispetto al totale dei rottami raccolti, costituisce una percentuale molto piccola e questo permette alle acciaierie di controllare il processo senza ridurre in modo significativo la qualità dell'acciaio ottenuto.
Banda cromata
La banda cromata è un’alternativa più economica della banda stagnata, ma offre una minore resistenza agli acidi e ha una limitata saldabilità. Lo strato protettivo è più sottile, ma più compatto. È utilizzata principalmente per coperchi, fondi, tappi corona, poiché non richiedono saldature.
Acciaio inossidabile
L’acciaio inossidabile utilizzato per la produzione di imballaggi è una lega che contiene cromo per almeno l’11%, che garantisce un’eccellente inerzia chimica e un’elevata resistenza alla corrosione. Questo tipo di packaging presenta inoltre un’alta resistenza meccanica e un’ottima lavorabilità.
Può essere di tre tipi diversi: austenitico, ferritico e martensitico, che si differenziano tra loro per le caratteristiche finali della lamiera.
Nel settore degli imballaggi, l’acciaio viene utilizzato nella produzione di barili, per esempio per la birra. Fusti in acciaio sono impiegati per lo stoccaggio e il trasporto di liquidi come l’olio o prodotti chimici come vernici e lubrificanti. Sempre per il trasporto, l’acciaio è anche utilizzato per la produzione di reggette.
In ambito industriale, grazie alla resistenza alle sollecitazioni meccaniche e alla pressione, l’acciaio viene utilizzato per la movimentazione di parti di macchine o strumenti.
Tipologie di imballaggi in acciaio
Nel settore degli imballaggi, secondo il Consorzio RICREA – Raccolta e Riciclo Imballaggi Acciaio, le principali strutture in acciaio possono essere suddivise in sei categorie, ciascuna caratterizzata da proprietà e scopi specifici.
Open top
L’espressione open top si riferisce a quegli imballaggi che presentano un’apertura nella parte superiore, come barattoli o scatolette metalliche. Realizzato in banda stagnata o cromata, questo tipo di packaging viene ampiamente impiegato per il confezionamento di prodotti alimentari, tra cui carne, pesce, frutta sciroppata e conserve vegetali, caffè e cibo per animali domestici.
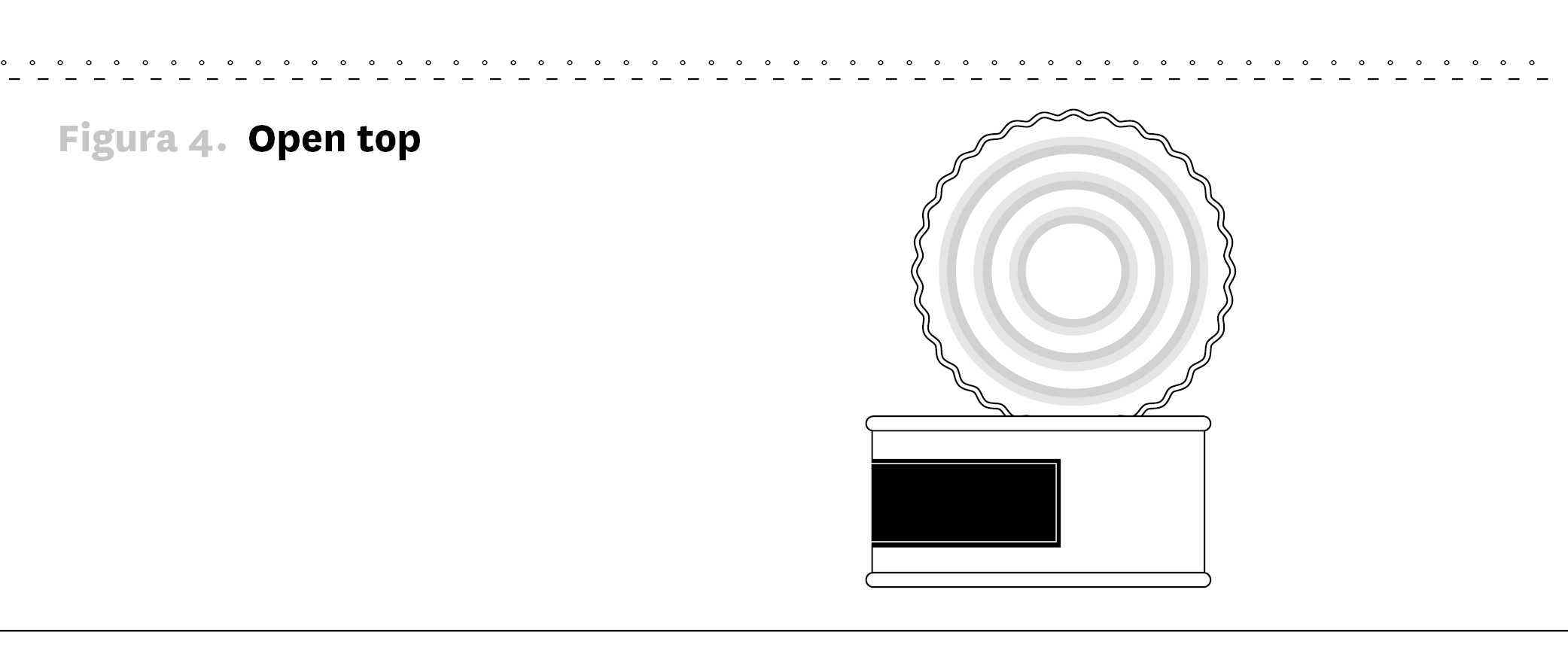
Questi imballaggi possono essere realizzati in tre pezzi, con un corpo principale, un fondello e un coperchio, oppure in due pezzi, con il corpo principale imbutito a cui viene successivamente applicato un coperchio. In entrambi i casi, con la diffusione dei sistemi di apertura facilitata, i coperchi vengono facilmente rimossi, anche quelli in altri materiali (per esempio, in alluminio).
Gli sforzi di ricerca e sviluppo nel settore hanno portato a un costante miglioramento delle prestazioni di questo tipo di imballaggi, ai quali l'industria ricorre da circa due secoli.
General line
In gergo tecnico, gli imballaggi indicati come “general line” sono contenitori realizzati tipicamente in banda stagnata. Sono disponibili in diverse forme, come cilindri e rettangoli, e offrono una grande versatilità per il confezionamento in base a requisiti specifici. Questo tipo di packaging viene utilizzato principalmente dall’industria chimica e da quella alimentare.
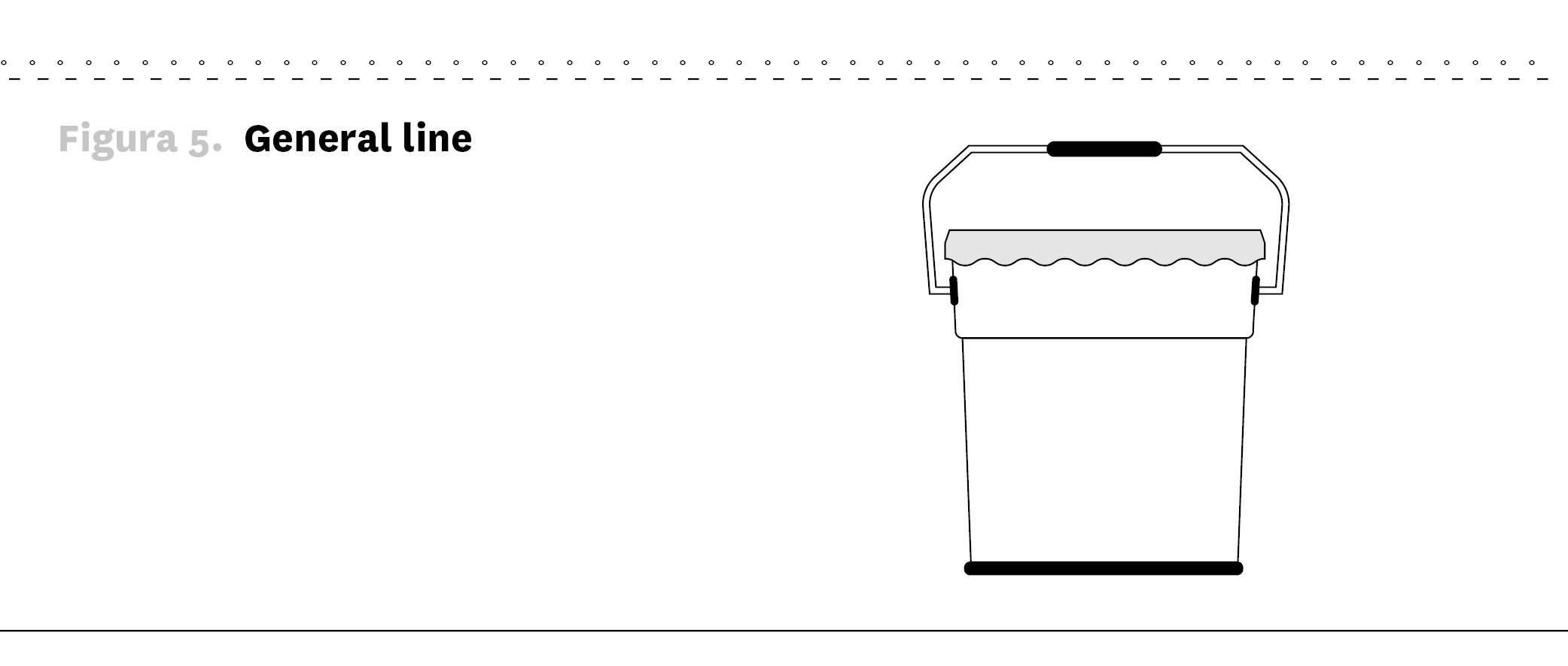
Grazie alla loro resistenza e durata, che li rendono adatti a contenere sostanze chimiche e prodotti corrosivi, questi imballaggi vengono impiegati per confezionare vernici, inchiostri, pitture, smalti, mastici e lubrificanti. Nell'industria alimentare, vengono apprezzati per le loro proprietà barriera all'ossigeno, all'umidità e alla luce, che contribuiscono a preservare la freschezza e la qualità dei prodotti.
La capacità di questi contenitori può variare, offrendo opzioni di confezionamento adatte anche per contenuti di volumi maggiori.
Chiusure
Le chiusure sono componenti essenziali degli imballaggi e sono progettate per garantire l'igiene, la sicurezza e l'integrità del prodotto contenuto.
Nel mercato esistono diverse categorie di chiusure in acciaio: tappi corona, capsule, coperchi, sigilli e gabbiette.
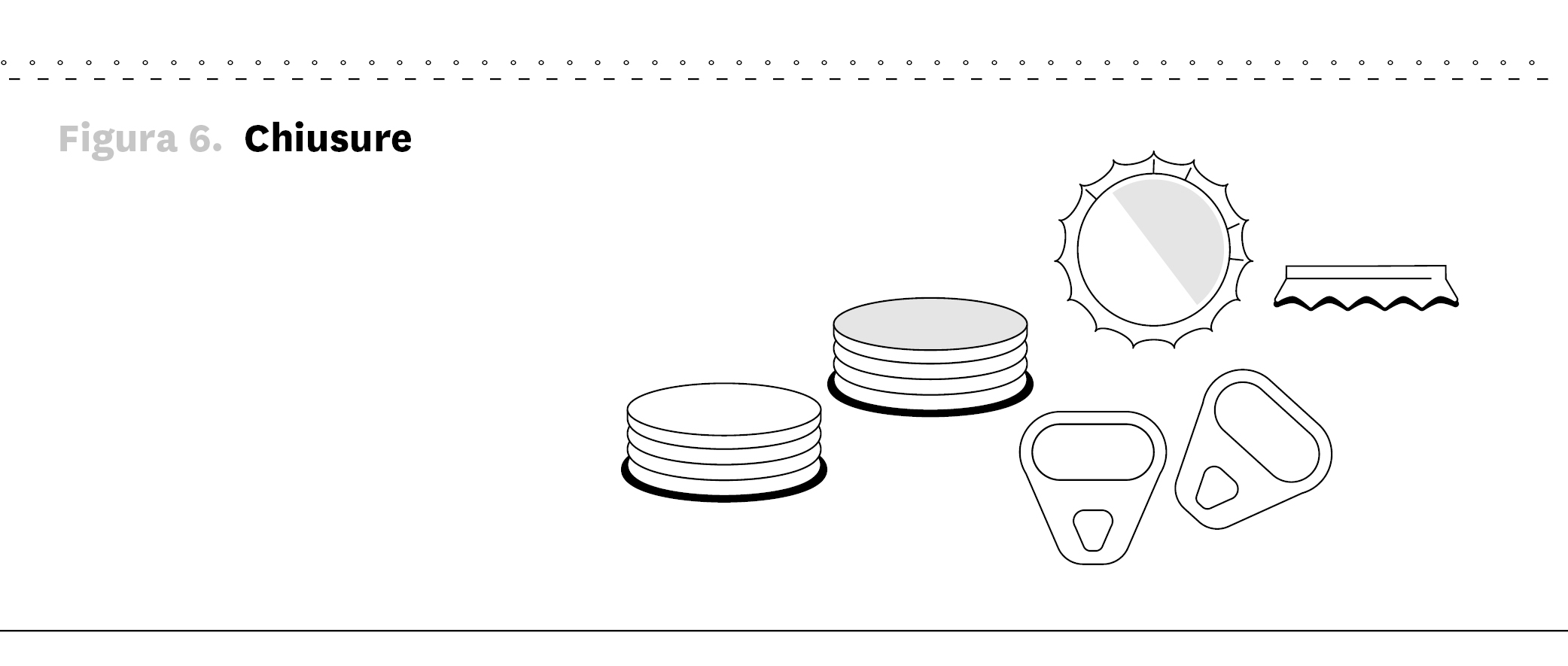
I tappi corona sono comunemente utilizzati per le bottiglie di vetro e sono utilizzati nell'industria delle bevande, per esempio, per confezionare la birra, le bibite gassate e l’acqua; offrono una chiusura ermetica che previene perdite di liquidi o gas.
Le capsule hanno un funzionamento analogo a quello dei tappi corona e sono impiegate per la chiusura di bottiglie in vetro e, in particolare, di barattoli. La filettatura interna consente di aprire e chiudere facilmente il contenitore, impedendo l’accesso all’aria o a contaminanti e preservando così la freschezza del prodotto.
I coperchi sono utilizzati per contenitori di varie forme, quali per esempio barattoli e secchielli in acciaio; possono essere dotati di sistemi di apertura facilitata, come anelli di trazione o linguette a strappo.
I sigilli, come etichette e nastri, vengono applicati alle giunzioni e alle chiusure per assicurare l'integrità del contenitore così come del contenuto; possono indicare se l'imballaggio è stato manomesso, fornendo una garanzia di autenticità e sicurezza.
Le gabbiette sono utilizzate per chiudere i fusti in acciaio nell'industria chimica e nel trasporto di liquidi o materiali sfusi; sono spesso dotate di maniglie o anelli di sollevamento, e garantiscono una chiusura sicura durante la movimentazione delle merci.
Bombolette aerosol
Le bombolette aerosol sono recipienti utilizzati per il confezionamento di sospensioni gassose e soluzioni liquide. Come propellenti, sempre più frequentemente sono impiegati il propano e il butano, che oltre ad avere un minore impatto ambientale garantiscono anche una maggiore facilità d'uso.
Sono solitamente realizzate in banda stagnata e richiedono una chiusura a pressione con valvola per erogare il prodotto; vengono realizzate mediante processi di formatura meccanica, che migliorano la loro resistenza alla pressione interna.
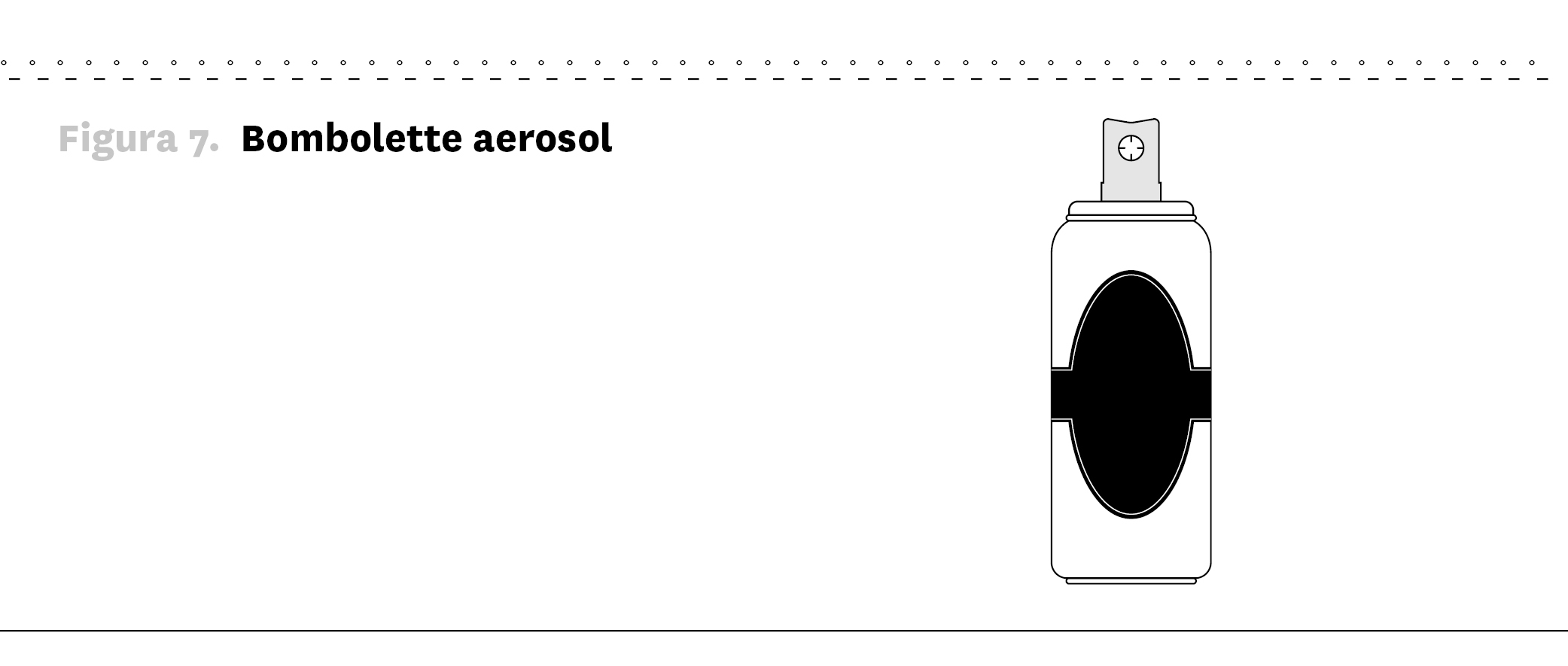
Le bombolette aerosol sono ampiamente utilizzate in vari settori per commercializzare prodotti di diverso tipo: articoli per la cura della casa, cosmetici, alimenti, insetticidi, farmaci e vernici.
Le bombolette aerosol possono essere smaltite facilmente, seguendo lo stesso processo di riciclaggio degli altri imballaggi in acciaio, anche se richiedono alcune attenzioni specifiche: da una parte, in fase di post-consumo, è fondamentale che il tappo erogatore, solitamente realizzato in plastica, sia correttamente separato dai consumatori e smaltito attraverso il sistema di raccolta differenziata; dall’altra, in fase di post-trattamento, occorre che gli operatori del riciclaggio prestino attenzione a possibili residui di gas compressi, che possono causare esplosioni, in particolare durante le operazioni di frantumazione per l’ottenimento di rottami di ferro.
Fusti
Fusti e barili sono contenitori realizzati in lamierino d’acciaio, con una capacità di immagazzinamento che può raggiungere i 250 litri. Questi recipienti sono utilizzati principalmente nel settore chimico e in quello petrolifero, ma trovano anche impiego nell’industria alimentare grazie a trattamenti superficiali specifici.
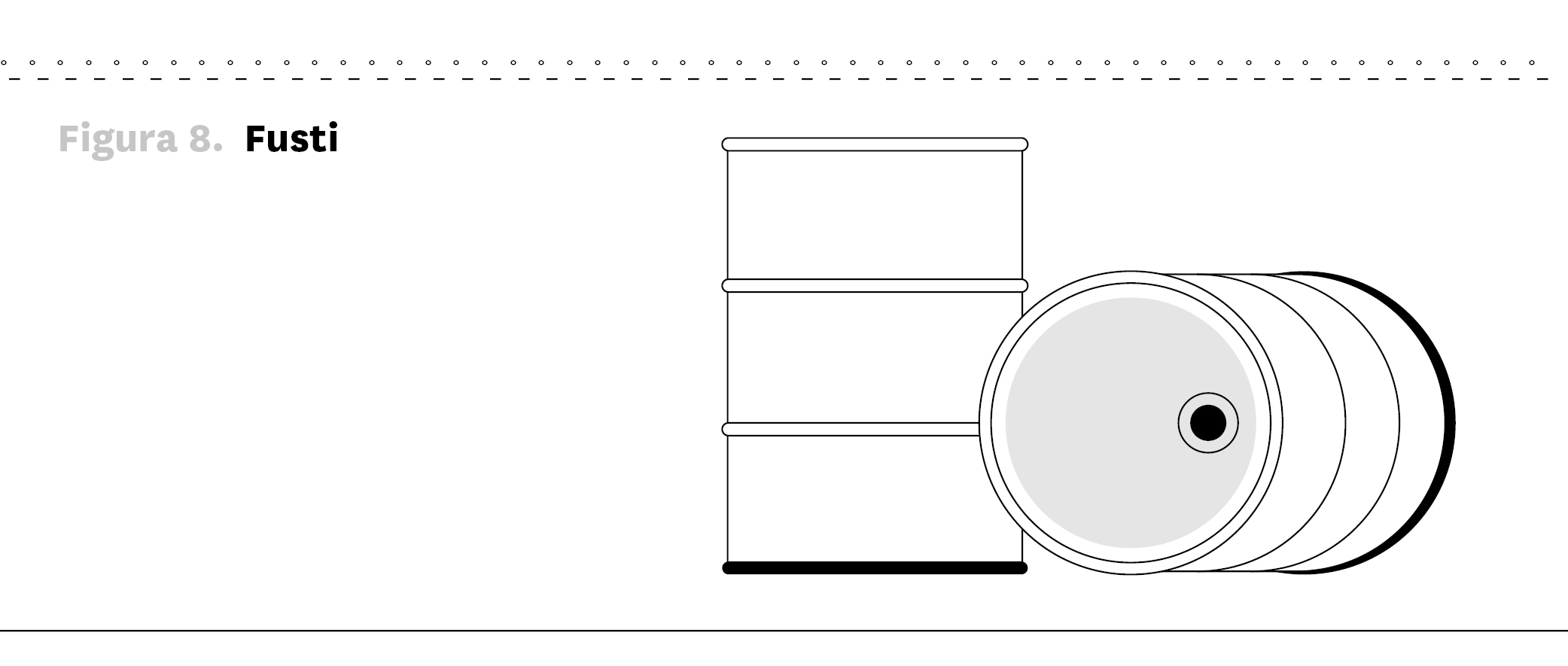
In questo caso vengono solitamente prodotti a forma di tronco di cono per facilitare l'impilamento e possono avere diversi metodi di chiusura a seconda del prodotto contenuto, liquido o solido. Abitualmente, sono realizzati con un acciaio basso-legato laminato a freddo e chiusi con saldature longitudinali; al loro interno, vengono rivestiti con lacche sintetiche protettive.
Prima di essere riciclati al termine del loro ciclo di vita, i fusti in acciaio possono essere riutilizzati più volte, dopo essere stati opportunamente trattati. Esistono in commercio anche soluzioni che prevedono l'aggiunta di un sacchetto interno in multistrato flessibile per il contenimento del prodotto; tale sacchetto, facilmente removibile e smaltibile separatamente, facilita il recupero e la rigenerazione dei fusti, poiché evita che questi ultimi entrino in contatto diretto con il contenuto e si sporchino.
Reggette e fili
Le reggette sono nastri sottili di metallo in rotoli, utilizzati come rinforzo per casse e scatole e per il fissaggio di carichi pesanti, come tubi, legname e prodotti per la movimentazione; sono, inoltre, impiegate con finalità antimanomissione. I fili sono utilizzati in alternativa alle reggette, spesso con le stesse finalità.
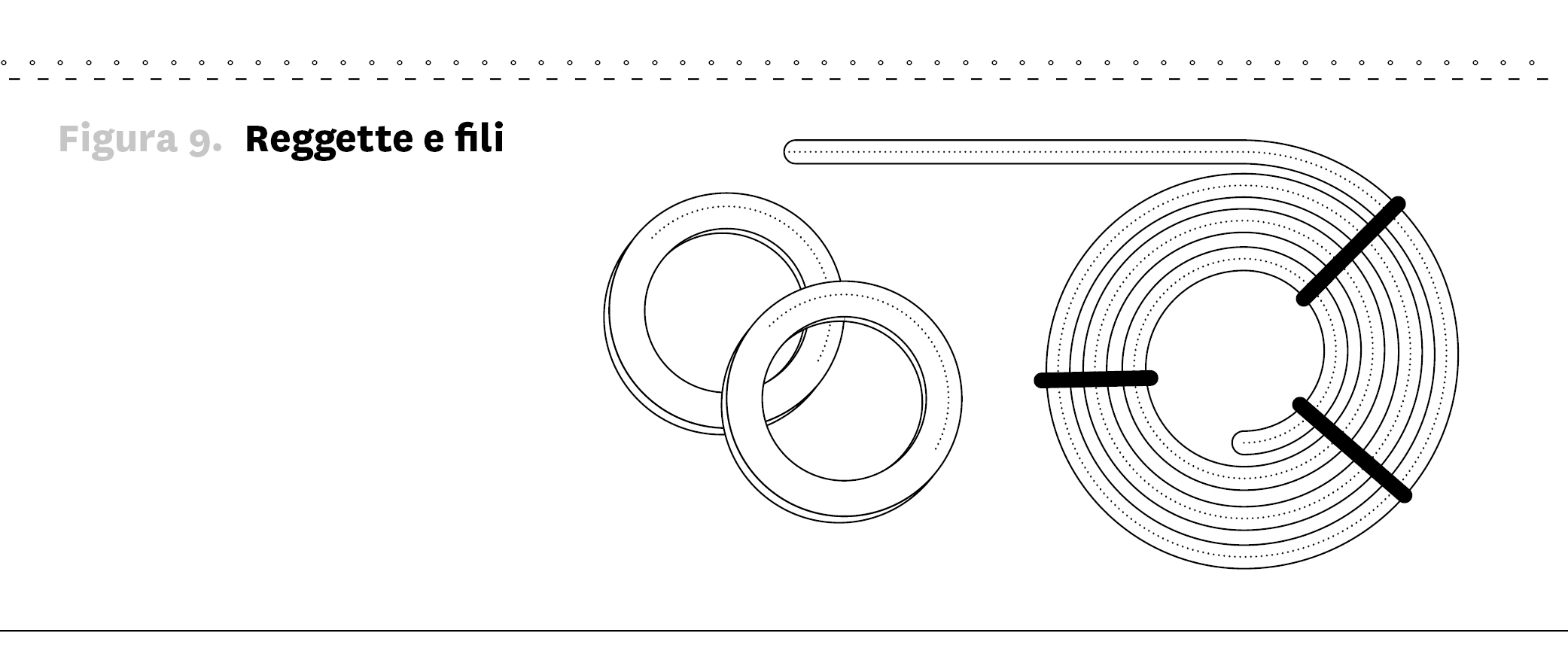
Il riciclo degli imballaggi in acciaio
Panoramica generale
Nella definizione di una soluzione di imballaggio, come già evidenziato, non si devono considerare solamente le funzioni comunicative e d'uso dell’oggetto, ma è necessaria una profonda consapevolezza dell'intero ciclo di vita del contenuto, così come del suo contenitore. Infatti, nel processo di progettazione non è solo fondamentale garantire un'efficace protezione del contenuto, la sicurezza del consumatore o un'adeguata promozione della marca, ma è anche importante tenere conto degli impatti ambientali e, più in generale, della sostenibilità degli imballaggi, in linea con le normative vigenti e in ottica di circolarità.
È quindi necessario un approccio sistemico alla progettazione di un packaging, che implichi, fin dalla sua concezione, la considerazione dei suoi impatti futuri sul sistema di raccolta, selezione e riciclo dei rifiuti. In altre parole, è opportuno che ogni progettista comprenda cosa accade quando un imballaggio raggiunge la fine della sua vita utile e deve essere gestito per essere adeguatamente riciclato. In questo modo, sarà possibile sviluppare soluzioni progettuali mirate per ottimizzare la gestione dei rifiuti, garantendo l'efficienza e la sostenibilità dei processi di riciclaggio.
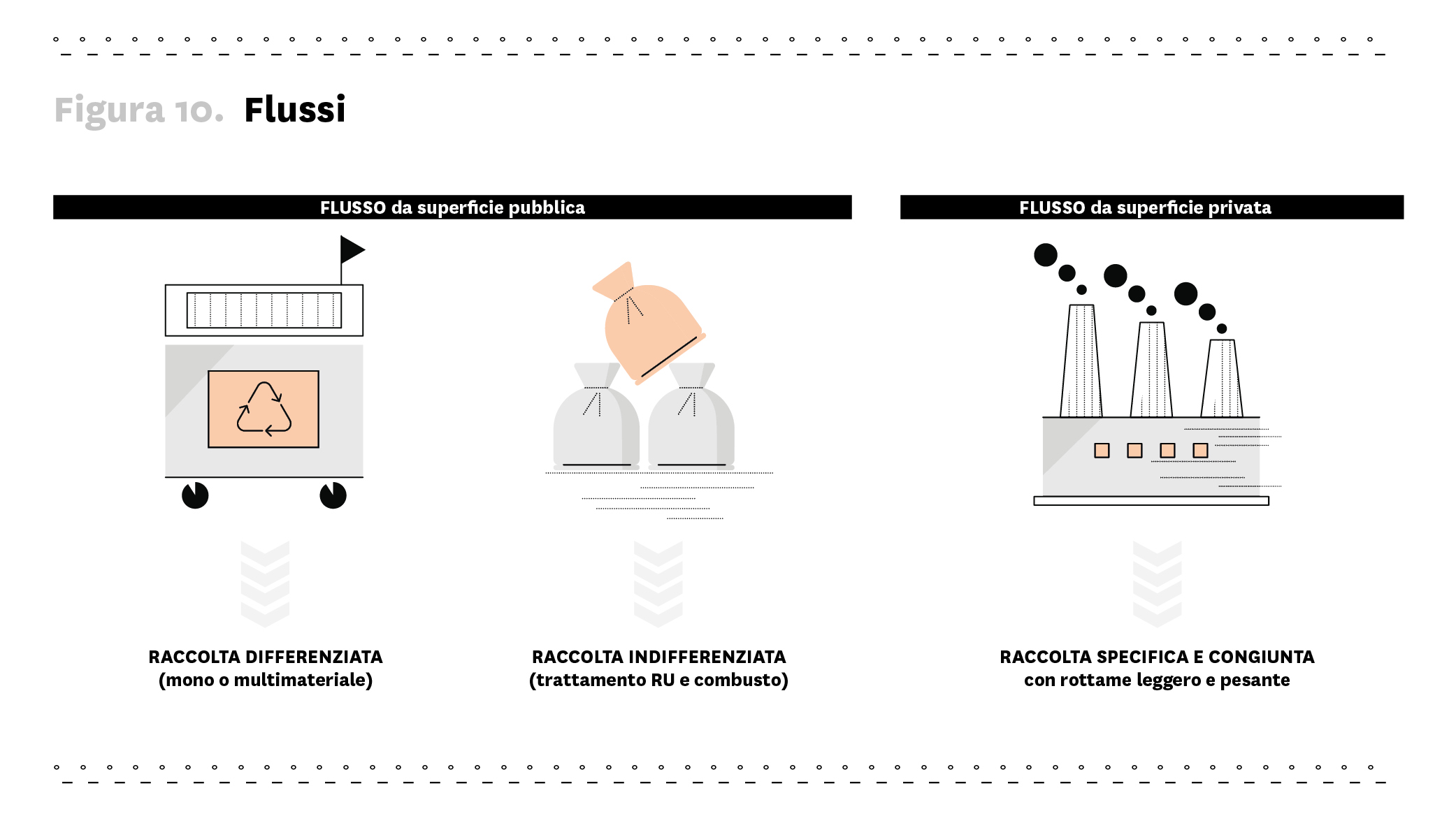
La descrizione della filiera del riciclo fornisce una panoramica completa delle fasi che gli imballaggi attraversano dopo il loro smaltimento come rifiuti da parte dei consumatori, fino alla loro trasformazione in materie prime seconde e alla loro reintroduzione nei processi produttivi. La conoscenza approfondita di queste fasi consente di ripensare gli imballaggi esistenti e di svilupparne di nuovi in un'ottica di circolarità e di innovazione sostenibile.
Questa pubblicazione si concentra in particolare sulla filiera degli imballaggi in acciaio per uso domestico e industriale.
Raccolta
La fase di avvio del processo di riciclo dei materiali ferrosi è costituita dalla raccolta, che può essere distinta in due flussi: da una parte, quello riferito alla gestione integrata dei rifiuti urbani, dall’altra, quello relativo agli imballaggi a uso industriale.
Il flusso urbano prevede:
- la raccolta differenziata monomateriale (solo imballaggi metallici);
- la raccolta differenziata multimateriale, che si differenzia in multimateriale leggera (quando vengono raccolti insieme metalli e plastica) e multimateriale pesante (metalli, vetro);
- la raccolta indifferenziata, dalla quale la frazione ferrosa può essere recuperata nel processo di trattamento meccanico biologico dei rifiuti residui, o dal trattamento delle ceneri pesanti dei termovalorizzatori, essendo la combustione un processo che non preclude la riciclabilità del materiale.
Il sistema maggiormente utilizzato in Italia è quello della raccolta differenziata multimateriale, che prevede la successiva separazione dei rifiuti raccolti in base agli specifici materiali. In questo quadro, le proprietà magnetiche dell’acciaio ne facilitano la separazione, assicurando una buona qualità del riciclato finale.
Per assicurare una raccolta differenziata dei rifiuti urbani di qualità è fondamentale sensibilizzare i cittadini affinché realizzino il corretto smaltimento degli imballaggi, contribuendo così a un efficace riciclo. Questa fase iniziale può essere determinante per il corretto svolgersi del processo così come del suo risultato finale. Già da diverso tempo sono in atto campagne educative da parte di comuni, associazioni e altre istituzioni, per fornire informazioni ai cittadini sulle buone pratiche associate alla raccolta differenziata.
Gli imballaggi a uso industriale vengono generalmente raccolti come rifiuto monomateriale, ma seguono poi un flusso che è a sua volta suddiviso in:
- rigenerazione imballaggi industriali riutilizzabili, quali fusti e cisternette;
- riciclo imballaggi industriali pericolosi non riutilizzabili;
- riciclo imballaggi industriali non pericolosi e non riutilizzabili;
- riciclo di reggetta e filo (assimilabile alla categoria precedente).
Separazione
La raccolta multimateriale richiede una adeguata separazione dei rifiuti al fine di renderli idonei ai processi di trattamento cui devono essere sottoposti per il recupero.
Il processo viene comunemente svolto presso appositi impianti di selezione. Il materiale viene inizialmente accumulato all’interno di un’area dove un gruppo di operatori procedono con una prima separazione manuale a terra, al fine di eliminare gli oggetti di maggiori dimensioni; vengono inoltre lacerati eventuali sacchetti e compattato il cumulo di rifiuti.
Successivamente a questa separazione preliminare, i diversi materiali vengono ulteriormente separati secondo passaggi progressivi attraverso varie stazioni.
Tra queste, è incluso tipicamente un impianto per la separazione magnetica mediante deferrizzatore: grazie a un magnete, vengono separati fisicamente i rottami ferrosi da quelli non ferrosi, che vengono convogliati su nastri trasportatori diversi.
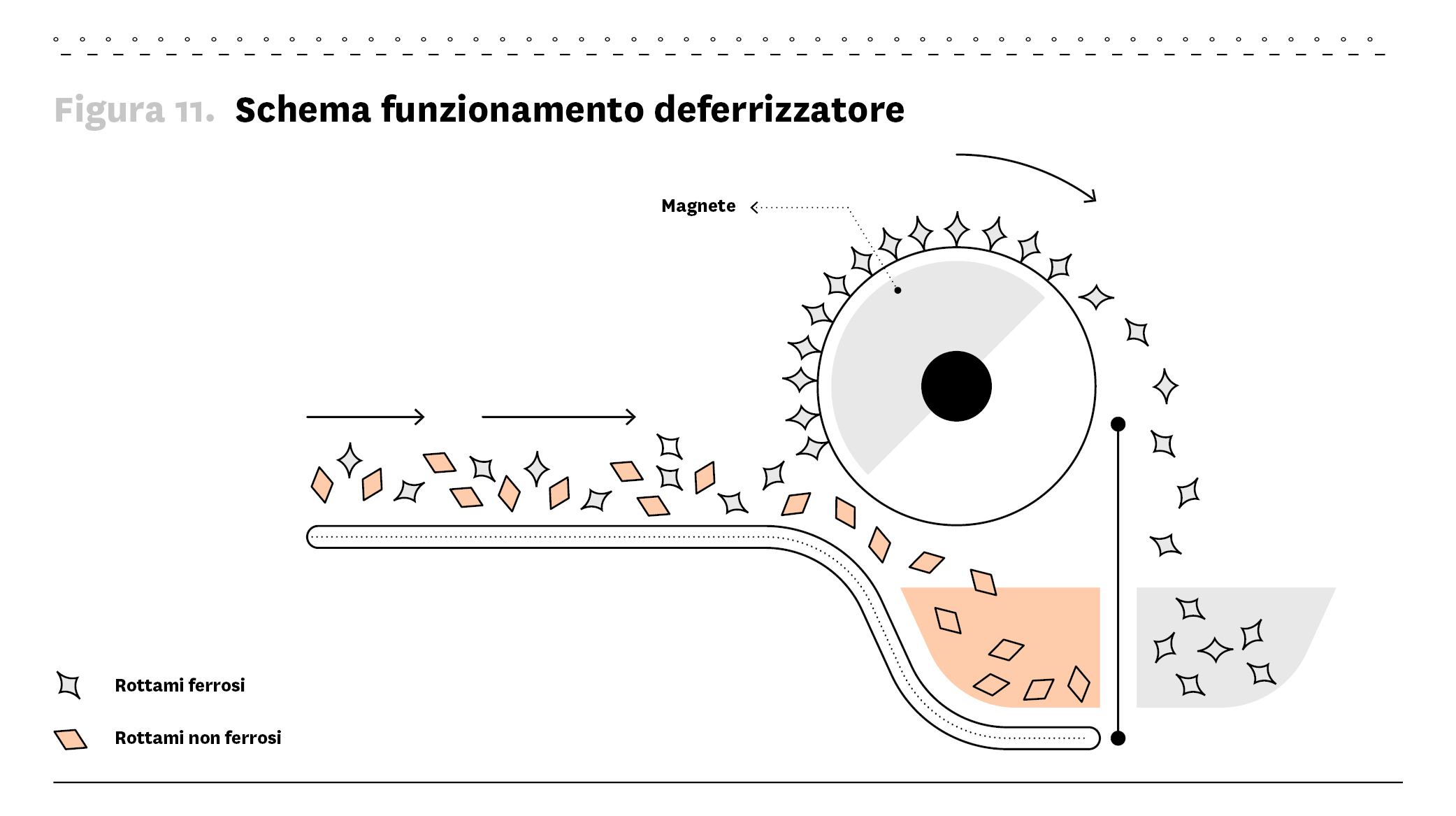
Per separare alcuni componenti metallici da altri non metallici, viene utilizzato anche un separatore a correnti parassite, che sfrutta le proprietà di conduzione elettrica dei metalli per isolarli da altri materiali.
Sono presenti, talvolta, stazioni dove è previsto nuovamente l’intervento manuale da parte di addetti che provvedono a separare particolari tipologie di rifiuti, come acciai di grandi dimensioni, plastiche o rifiuti considerati critici, quali confezioni sigillate e materiali non riciclabili. Questa operazione riveste un ruolo di grande delicatezza in quanto consente di ottimizzare l’intero processo.
Alla fine del processo, per mezzo di nastri trasportatori, ciò che è stato smistato viene stoccato in diverse aree, ognuna designata per un materiale specifico: acciaio, alluminio, plastica, vetro e rifiuti organici.
Trattamento
Dopo la fase di separazione il rottame da imballaggio necessita di essere trattato prima di poter essere riciclato in acciaierie e fonderie; le lavorazioni previste in questa fase consentono sia di ridurre il volume complessivo dei rottami sia di migliorarne la qualità.
Nell’ambito del trattamento esistono due possibili procedure, tra loro alternative, che sono parte del processo complessivo: da un lato la frantumazione, dall'altro la vagliatura e la pressatura, che hanno in comune sia la fase iniziale sia quella finale. In entrambi i casi, infatti, i rottami vengono conferiti agli impianti di trattamento, i quali, mediante specifica strumentazione tecnica, valutano il peso, la qualità del materiale ricevuto e la presenza di eventuali parti non conformi, rilevate anche grazie a portali radiometrici che identificano eventuali elementi radioattivi.
All’inizio del processo di trattamento, che è di tipo semi-automatizzato, il materiale in entrata viene introdotto in una tramoggia e, tramite nastri trasportatori, fatto transitare attraverso le diverse stazioni che si occupano di affinarne progressivamente la qualità. In caso di disomogeneità o presenza all’interno del flusso di materiale di elementi non idonei a questo processo, quali per esempio elementi non riciclabili o di profili particolarmente lunghi, è sempre previsto un intervento umano, analogamente alla fase di separazione.
Successivamente, come già anticipato, a seconda dell’impianto di trattamento è possibile seguire due procedure alternative.
Una prima opzione è costituita dalla frantumazione, che prevede che il rottame precedentemente selezionato venga appunto frantumato mediante un mulino, al fine di ottenere scaglie di dimensioni ridotte (proler), tali da poter accedere alle fasi successive del processo di trattamento. In questa operazione vengono inoltre rimosse le impurità, quali elementi organici e inclusioni non ferrose.
A seguito delle procedure di frantumazione, la fase finale del processo prevede che i rottami siano oggetto di altri due trattamenti: deferrizzazione e separazione aeraulica. Il primo separa dal flusso di materiali le parti in ferro, grazie alle loro proprietà magnetiche, analogamente a quanto già visto per la fase di separazione. Il materiale così ottenuto può, tuttavia, presentare delle impurità non metalliche, per esempio in carta o in plastica, che possono restare incastrate o attaccate. Per eliminare tali impurità il materiale viene sottoposto a separazione aeraulica, che consiste nell’utilizzo di getti d’aria per rimuovere gli elementi più leggeri.
In alternativa alla frantumazione il rottame viene fatto passare all’interno di un vaglio rotativo, composto da un tamburo cilindrico montato su un asse inclinato che ruota su se stesso. Attraverso opportune forature i rottami di piccole dimensioni (per esempio, tappi ed elementi non metallici) vengono filtrati e separati dal flusso principale; i rottami di dimensioni maggiori rimangono in superficie e vengono spinti verso il punto finale del tamburo. A differenza della prima procedura, che prevede la riduzione del volume dei rottami proprio in virtù della frantumazione stessa, a valle della vagliatura è anche prevista una fase finale di pressatura, che comprime i materiali per ridurne le dimensioni.
In alcune circostanze, i rottami in banda stagnata possono anche essere sottoposti a un processo di distagnazione, che consente di separare lo stagno. Lo stagno può pregiudicare i processi di fusione dell’acciaio, anche se quantità controllate sono considerate accettabili dalle acciaierie che dosano la quantità di banda stagnata all’interno della fusione. Prima della separazione dello stagno il materiale deve essere depurato per rimuovere gli elementi estranei ed evitare l'inquinamento dei bagni alcalini utilizzati nel processo. Oltre al recupero dello stagno, il processo produce un rottame di ferro di migliore qualità.
Infine, il materiale processato viene stoccato in diversi depositi. Può essere suddiviso in rottami pronti per essere inviati alle acciaierie; rottami con una percentuale significativa di altri materiali, che subiscono un ulteriore ciclo; e scarti costituiti principalmente da plastica residua e rifiuti organici, destinati allo smaltimento.
Nel materiale finale rimane una quantità minima di rifiuti non metallici, che deve essere inferiore al 2% secondo il Regolamento (UE) n. 333/2011 del Consiglio del 31 marzo. Si tratta principalmente di plastica, carta e altri elementi che rimangono incastrati tra i pezzi triturati. Tuttavia, questa quantità non crea problemi durante la fusione del materiale in acciaieria e in fonderia.
Un aspetto importante da tenere in considerazione è che i materiali ferrosi perdono lo status di rifiuto una volta che sono stati oggetto di specifici processi di trattamento per essere catalogati in materia prima seconda. Per una definizione precisa di queste condizioni, si rimanda alla normativa di riferimento, specificamente il Regolamento (UE) 33/2011.
Fusione
La fusione rappresenta la fase finale del processo complessivo fin qui descritto. È questa la parte in cui avviene il vero e proprio riciclo dell’acciaio, cioè la trasformazione dei rottami ferrosi in materia prima seconda all'interno di un impianto siderurgico.
I rottami selezionati per la fusione vengono, quindi, pesati ed eventualmente addizionati con altri elementi di lega, con l’obiettivo, per esempio, di correggere il tenore di carbonio o di aggiungere altri metalli per modificare la composizione della materia prima seconda che si desidera ottenere.
Successivamente, il materiale viene caricato e introdotto all’interno del forno elettrico per la sua fusione, che avviene attraverso un processo continuo e in diversi step.
Questa fase rappresenta il momento di maggior consumo energetico dell'intero processo; infatti, il forno elettrico viene portato a una temperatura di circa 1500-1.600 °C, necessaria per la fusione dell'acciaio. Grandi conduttori di grafite vengono attivati per generare il calore necessario a mantenere la temperatura stabile. Ogni ciclo di fusione ha una durata di circa 5 minuti, durante i quali vengono fuse approssimativamente 50 tonnellate di materiale.
Prima di estrarre l'acciaio fuso vengono rimosse le scorie di produzione, che presentano una densità inferiore rispetto all'acciaio e affiorano in superficie; per ottenere la densità appropriata per separarle dall’acciaio fuso vengono aggiunti al materiale di colata specifici polimeri. Le scorie vengono, quindi, separate e depositate in ceste di raffreddamento, per essere successivamente trattate e trasformate in materiale inerte, spesso impiegato in edilizia come alternativa alla ghiaia.
L'acciaio fuso, dopo la rimozione delle scorie, subisce poi ulteriori fasi di lavorazione per migliorare le sue proprietà meccaniche attraverso l'aggiunta di altri elementi; una parte del materiale fuso viene mantenuta all'interno del forno per ottimizzare la colata successiva. Segue, quindi, l'estrusione e il raffreddamento mediante spruzzatura di acqua dei semilavorati finali, che generalmente assumono la forma di billette, utilizzate principalmente nell'industria delle costruzioni.
La fusione richiede grandi quantità di acqua per il raffreddamento del materiale in uscita e per il trattamento dei sottoprodotti come gli ossidi; per limitare il consumo di acqua, questa viene reintrodotta nel ciclo produttivo dopo essere stata opportunamente processata.
Oltre a richiedere grandi quantità di acqua la fusione è anche un processo, come già detto, estremamente energivoro; ha quindi impatti ambientali significativi in termini di consumo di risorse e di emissioni. Tuttavia, nel corso degli anni, sono stati intraprese azioni mirate a ridurre o compensare questi impatti, attraverso, ad esempio, l'adozione di filtri per purificare l'aria e ridurre le emissioni di gas serra, o l'utilizzo del calore generato dalla fusione per riscaldare gli uffici associati agli impianti e fornire energia termica ai comuni limitrofi.
Trattamento degli imballaggi pericolosi
La raccolta e il trattamento degli imballaggi classificati come pericolosi, seguono una filiera dedicata che fa uso di procedure specifiche allo scopo di bonificarli, eliminandone gli agenti nocivi. L'appellativo “pericoloso” si riferisce a un’ampia gamma di sostanze che presentano un pericolo significativo sia per l'incolumità umana che per l'ambiente: sostanze esplosive, infiammabili, irritanti, corrosive, tossiche o cancerogene.
La bonifica permette di garantire un’elevata qualità del materiale in uscita (proler), con una quota approssimativa del 99% di rottame in acciaio; tale risultato è assicurato se i rottami in entrata sono quasi interamente ferrosi.
Gli imballaggi conferiti negli impianti specializzati possono contenere una percentuale residua di rifiuto pericoloso: al fine di assicurare la massima efficienza e sicurezza, il materiale di scarto viene sottoposto a una dettagliata analisi all’ingresso volta a individuare la presenza di imballaggi sigillati e chiusi o materiale radioattivo, che vanno opportunamente trattati prima di essere immagazzinati.
Possono essere impiegate due differenti procedure: la pulitura per attrito e la pulitura con solventi.
La pulitura per attrito è simile al processo di frantumazione già visto in precedenza, ma utilizza una strumentazione opportunamente modificata per consentire, grazie all’effetto di forte attrito, di separare la sostanza pericolosa dal rottame. Data la pericolosità intrinseca delle sostanze coinvolte, il controllo attento e la riduzione opportuna della temperatura di esercizio durante la pulitura per attrito costituisce un aspetto cruciale al fine di prevenire l’insorgere di fiamme libere e scoppi. Inoltre, vengono aspirati eventuali gas e polveri sottili generati durante il processo.
Nella pulitura con solventi vengono invece utilizzati dei sistemi semi-automatizzati che, per rimuovere dagli imballaggi le sostanze nocive, utilizzano acqua e solvente. Per i casi più critici si predilige l’uso di solvente vergine, mentre per gli altri casi può essere utilizzato solvente già impiegato per altre puliture che mescolato con un 30% di componente vergine; questa composizione viene, inoltre, definita di volta in volta per meglio agire in sicurezza sul prodotto. Il solvente esausto e non più riutilizzabile viene recuperato e rigenerato nell’impianto stesso.
Rigenerazione degli imballaggi industriali
Alcuni imballaggi a uso industriale, quali fusti e cisternette a gabbia metallica, possono essere rigenerati, ovvero sottoposti a un processo che consente di ripristinare le loro condizioni originali, anche quando hanno contenuto sostanze nocive o pericolose. In questo modo è possibile evitare la fusione di materiale per l’ottenimento di nuovi contenitori, con un importante risparmio di energia e riduzione di emissioni climalteranti.
Si stima che la rigenerazione riesca a garantire da sette a dieci riutilizzi un fusto nell’arco della sua vita utile e che si abbia un importante risparmio di risorse già dal suo secondo utilizzo.
Spessore dei fusti
La riduzione del peso dell’imballaggio a parità di prestazioni è sicuramente un elemento che consente di conseguire gli obiettivi di diminuzione del consumo di risorse naturali e di limitazione degli impatti negativi sull’ambiente. Bisogna considerare, però, che l’attenzione volta a ridurre il peso degli imballaggi deve essere contemperata con il mantenimento delle caratteristiche funzionali a garantire le possibilità di riutilizzare il fusto dopo il primo ciclo d’uso.
Sul mercato italiano vengono immessi fusti in acciaio più leggeri rispetto a quelli impiegati in altri Paesi e ciò si traduce in un incremento dei danneggiamenti degli imballaggi in fase d’uso e in una riduzione della possibilità di riutilizzarli, rigenerarli e prepararli per il riutilizzo, soprattutto nel caso in cui si tratti di imballaggi che richiedono un’omologazione.
Il bilancio ambientale più favorevole si raggiunge quando lo spessore della lamiera della pancia del fusto è pari ad almeno 0,9 millimetri e quello del coperchio ad 1 millimetro. Fusti con spessori inferiori, pur essendo stati immessi sul mercato come imballaggi riutilizzabili, rischiano di diventare imballaggi monouso, con evidentemente drastico peggioramento delle prestazioni ambientali degli stessi lungo il ciclo di vita del prodotto.
Dal punto di vista del peso complessivo del fusto, il valore sotto il quale è indispensabile non scendere per assicurare una pluralità di cicli d’uso dell’imballaggio è pari a 15,5-16 kg.
Standardizzazione
L’obiettivo costituito dall’incremento del tasso di riutilizzo e di rigenerazione dei fusti in acciaio richiede una maggiore standardizzazione dei prodotti: tappi posti a distanze diverse e formati anomali costituiscono altrettanti elementi di riduzione della possibilità di rigenerazione degli imballaggi.
Elementi costruttivi
Altri fattori decisivi per il miglioramento della possibilità di rigenerazione dei fusti sono costituiti dalla qualità della laccatura, che è necessario mantenere ad elevati livelli qualitativi, e dalla tripla aggraffatura in luogo di quella doppia.
Rigenerazione dei fusti
Il processo di rigenerazione di un fusto si svolge come segue.
La fase iniziale prevede un controllo dell’imballaggio. Alcuni contenitori, anche se apparentemente vuoti, possono avere al proprio interno dei residui che devono essere pretrattati per evitare che causino delle possibili reazioni con i solventi durante il lavaggio. Il controllo dei fusti avviene per lotti della stessa azienda, in modo da poter trattare in modo specifico gruppi di contenitori.
Nel caso in cui sia stato a contatto con sostanze pericolose, come oli, resine e vernici, il fusto necessita di una fase di prelavaggio con acqua e soda oppure con un solvente. Il processo di pulitura del fusto varia anche in funzione della chiusura che lo caratterizza. Ad esempio, se il fusto presenta un’apertura parziale, ossia con tappo, indica che ha contenuto liquidi come oli, vernici, diluenti o lubrificanti, se invece presenta un’apertura parziale, ossia tappo mobile, esso ha contenuto polveri o paste. Le acque reflue prodotte in questa fase e l’aria esausta aspirata dalle cabine di lavaggio vengono depurate e i residui che rimangono nel fusto vengono aspirati e portati a incenerimento.
Successivamente alla pulitura viene effettuato il ripristino della forma del fusto, che consiste in un risanamento dei bordi e di possibili ammaccature; è una fase altamente automatizzata.
Come fase finale della rigenerazione viene effettuata una spazzolatura esterna del fusto per rimuovere etichette e altri adesivi e viene realizzata una verniciatura per uniformarne la superficie del contenitore.
Come fase finale della rigenerazione viene effettuata una spazzolatura esterna del fusto per rimuovere etichette e altri adesivi e viene realizzata una verniciatura per uniformare la superficie.
Nel caso di fusti che al proprio interno presentano uno strato in polietilene per il contenimento di specifiche sostanze pericolose, una volta eliminato il componente in plastica viene recuperata la struttura in acciaio.
Tutto il processo è progettato per ridurre al minimo gli sprechi. I solventi e l'acqua utilizzati durante il processo vengono periodicamente depurati e riutilizzati, contribuendo così a una gestione sostenibile del processo industriale.
I fusti scartati per la rigenerazione o al termine della loro vita utile vengono avviati a recupero di materiale attuando una riduzione volumetrica per facilitarne il trasporto verso gli impianti di riciclo, diventando così rottame ferroso destinato a fusione.
Rigenerazione delle cisternette
Il processo di rigenerazione delle cisterne a gabbia metallica avviene in modo simile a quello dei fusti.
Al fine di individuare eventuali criticità sia nella gabbia metallica che nell'otre in plastica, viene effettuata un'ispezione preliminare, in base alla quale i contenitori vengono selezionati per essere sottoposti a pulitura.
Nel caso in cui l'otre di plastica non possa più essere riutilizzato a causa della permeazione di materiale pericoloso o di ammaccature non recuperabili, viene sostituito con un nuovo contenitore; allo stesso modo, nel caso delle gabbie metalliche, i loro bordi vengono ripristinati e le ammaccature riparate quando possibile.
Come per i fusti, anche le cisternette vengono pulite con solventi la cui composizione viene definita in relazione al tipo di prodotto precedentemente contenuto. Successivamente i contenitori vengono asciugati per aspirazione o ad aria.
Le parti non rigenerabili vengono riciclate, a tal fine vengono tagliate e frantumate fino a raggiungere la pezzatura necessaria; in questo processo è compresa anche una fase di lavaggio per rimuovere tutte le sostanze a contatto con il materiale.
Indicazioni progettuali per la facilitazione delle attività di riciclo degli imballaggi in acciaio
Principi generali
La facilitazione delle attività di riciclo rappresenta, come sottolineato da CONAI, una delle principali leve di prevenzione per la riduzione degli impatti ambientali derivanti dai rifiuti di imballaggio. Attraverso il riciclo, i rifiuti generati da un processo produttivo possono diventare una risorsa preziosa per lo stesso o per altri processi, offrendo evidenti vantaggi ambientali, ma anche portando ad un uso ottimizzato delle risorse con conseguenti benefici economici.
In questo quadro, chi progetta gioca un ruolo essenziale, ad esempio rispetto a scelte orientate alla monomaterialità o a una più facile separazione dei diversi componenti, come etichette, chiusure ed erogatori. Grazie a interventi progettuali attenti e consapevoli, diventa possibile rendere la produzione degli imballaggi sempre più allineata a modelli di economia circolare.
I paragrafi che seguono presentano alcune linee guida per sviluppare packaging in acciaio in un'ottica di prevenzione e di facilitazione delle attività di riciclo, offrendo uno strumento sia per analizzare e valutare imballaggi esistenti sia, soprattutto, per progettarne di nuovi. Le indicazioni presentate in questo documento intendono supportare progettisti e imprese nella definizione di contenitori, siano essi destinati ai consumatori finali o agli operatori industriali, che siano concepiti non solo in funzione del proprio contenuto, dei contesti di produzione, trasporto, vendita e consumo, ma anche tenendo conto di ciò che accadrà post-consumo, cioè quando si trasformano in rifiuti e devono essere smaltiti.
Prevedere cosa accadrà nella fase di smaltimento significa concretamente capire quali attività sono previste dalla filiera del riciclo, quali tecnologie sono attualmente disponibili e quali processi industriali sono utilizzati negli impianti in funzione in Italia, al fine di immettere sul mercato imballaggi che siano compatibili con il sistema nel suo complesso.
In fase di progettazione, occorre dunque considerare gli aspetti appena citati, bilanciandoli con un’attenta valutazione delle caratteristiche del prodotto che l'imballaggio deve contenere e delle esigenze espresse dal sistema di attori e dalle fasi della filiera in cui è inserito. Infatti, il rispetto dei requisiti di protezione e conservazione del contenuto, nonché di sicurezza per il consumatore, di conformità alle normative e di compatibilità con il sistema produttivo e logistico, deve essere accompagnato da una particolare attenzione alla riciclabilità, alla semplificazione delle forme complesse, alla riduzione dei trattamenti speciali non strettamente necessari e così via, in modo da facilitare le attività di riciclaggio, ma senza compromettere la salvaguardia del prodotto e il funzionamento dei processi, evitando sprechi e di conseguenza un inutile consumo di risorse.
Strettamente correlato alla riduzione degli sprechi è, ad esempio, il tema della porzionatura. Questa pratica, particolarmente rilevante per gli imballaggi alimentari, tiene conto dei cambiamenti sociali e della progressiva riduzione del numero di componenti dei nuclei familiari: Il confezionamento in porzioni più piccole evita di fatto lo spreco di cibo rispetto ai formati più grandi, che a volte sono difficili da consumare interamente entro la scadenza, soprattutto per le persone che vivono da sole. Facilitare il riciclo non significa quindi rifiutare a priori alcuni tipi di soluzioni progettuali, ma piuttosto calibrare un complesso sistema di fattori inerenti al rapporto tra contenuto, contenitore e processi associati. Mantenendo un equilibrio tra i requisiti funzionali dell'imballaggio e le considerazioni ambientali, è possibile produrre imballaggi che soddisfino i requisiti di sicurezza, preservino l'ambiente e promuovano l’economia circolare.
Le indicazioni contenute si basano sull’osservazione del comportamento dell'imballaggio e di tutti i suoi componenti lungo l’intero percorso che porta dalla raccolta differenziata alla produzione della materia prima seconda. Considerando i processi di selezione e riciclo comuni a diverse categorie di imballaggi, sono stati esaminati i seguenti aspetti: svuotamento ed eliminazione di residui, dimensione strutturale e componenti, trattamenti superficiali, informazioni ambientali e sensibilizzazione degli utenti finali.
Anche se non è possibile stabilire linee guida assolute e indicare regole valide per tutte le situazioni che possono verificarsi in questo settore, questo documento ha l’obiettivo di presentare delle raccomandazioni e dei consigli generali che stimolino la ricerca di soluzioni di imballaggio più facilmente riciclabili. Data la varietà di tipologie di imballaggi in acciaio, ogni situazione specifica richiede una valutazione mirata, che tenga conto dei requisiti normativi, funzionali, comunicativi e ambientali di ogni confezione.
Aspetti strutturali
A livello di progettazione, la struttura del packaging gioca un ruolo fondamentale in termini di funzionalità, sia per quanto riguarda la protezione del contenuto che l'ergonomia d'uso, agevolando la manipolazione e la fruizione del prodotto da parte dell'utente finale.
Tuttavia, nel definire gli aspetti strutturali dell'imballaggio, è importante considerare come la scelta di una determinata morfologia o di determinati spessori possa incidere significativamente non solo sulle prestazioni ma anche sull’impatto ambientale (consumo di risorse ed emissioni) del packaging, sia in fase di produzione (impiego di materia prima), sia durante il trasporto (per il peso e lo spazio necessario per lo stoccaggio), sia nella gestione del fine vita.
Pur garantendo che le prestazioni e i requisiti funzionali dell'imballaggio siano sempre soddisfatti, è quindi necessario fare scelte progettuali che riducano il più possibile gli impatti, per esempio riducendo i volumi e gli spessori della struttura del packaging. In questo senso, per bilanciare la riduzione del materiale con la garanzia di resistenza meccanica del packaging, ad esempio per assicurare un'adeguata impilabilità con conseguenti benefici in termini di logistica, è possibile intervenire sulla morfologia dell'imballaggio modificandone le geometrie del profilo (ad esempio, aggiungendo nervature) e rafforzando così la struttura complessiva.
Un altro aspetto da considerare è che le forme con sezioni trasversali variabili, soprattutto con profili estremamente pronunciati, possono incastrarsi con altri rifiuti al momento del conferimento; per questo motivo, è preferibile privilegiare forme regolari, in quanto la variazione della sezione trasversale può influenzare il processo di riciclo.
Infine, è consigliabile, quando possibile, optare per soluzioni che consentano una più facile manipolazione dell'imballaggio in acciaio da parte dell'utente: oltre a favorire l'accesso e il consumo del prodotto, è possibile agevolare le operazioni di riciclo progettando l'imballaggio in modo che nella fase post-consumo sia semplice separare i componenti nonché compattare e ridurre il volume delle confezioni.
In sintesi, a parità di prestazioni, è preferibile:
- ridurre il più possibile spessori e volumi dell’imballaggio garantendone sempre la sicurezza e le prestazioni, per esempio la resistenza meccanica nell’impilamento;
- semplificare la forma dell'imballaggio e prediligere delle morfologie con variazioni di sezione non particolarmente pronunciate;
- facilitare la manipolazione sicura dell’imballaggio da parte dell’utente, in modo da favorire la compattazione e la riduzione di volume prima del conferimento nella raccolta differenziata.
Componenti
Nella valutazione complessiva della struttura dell'imballaggio, un altro aspetto da tenere in considerazione in una progettazione orientata a facilitare le attività di riciclo è la relazione tra il corpo principale dell'imballaggio e i suoi componenti accessori. È comune incontrare imballaggi in acciaio con componenti secondari di materiali diversi o, al contrario, imballaggi di altri materiali contenenti parti in acciaio.
La mescolanza di più materiali può compromettere il riciclo, soprattutto quando i componenti sono difficili da separare. La presenza, per esempio, di componenti in plastica rigida non removibili, come nel caso dei manici dei secchielli, potrebbe essere un potenziale ostacolo al riciclo, per questo, per quanto possibile, sarebbero da evitare o per lo meno ridurne al minimo la presenza rendendoli facilmente asportabili.
Per ridurre al minimo gli inconvenienti e ottimizzare il processo di riciclo, si raccomanda quando possibile la riduzione del numero di componenti e l’adozione di soluzioni monomateriale; tuttavia, nelle situazioni in cui ciò non sia possibile, è necessario progettare i componenti in modo che siano facilmente separabili dall'utente finale, in modo da essere correttamente conferiti nella raccolta differenziata. La comunicazione, in questo senso, gioca un ruolo fondamentale nell'orientare il consumatore a riconoscere i vari materiali e a smaltirli correttamente, contribuendo così a un riciclo efficiente.
Se realizzati in materiali diversi dall'acciaio, componenti come tappi e chiusure, dispenser, valvole o etichette, devono quindi essere progettati tenendo conto della loro separabilità, prevedendone il comportamento durante tutto il ciclo di vita dell'imballaggio, non solo nelle fasi iniziali fino al consumo del prodotto, ma anche in quelle successive per un adeguato smaltimento.
Potenziali criticità emergono quando si utilizza PVC adeso a tappi o chiusure in acciaio, poiché la combustione del PVC insieme ai componenti metallici all’interno del forno può produrre fumi tossici. Questa tossicità deriva dalla presenza di cloro nel polimero, che durante la combustione forma sostanze pericolose come l’acido cloridrico. Come abbiamo visto nel capitolo precedente, l’impianto di fusione opera a temperature molto elevate, tale temperatura permette la separazione del cloro dal PVC sotto forma di acido cloridrico gassoso. L’industria della produzione degli imballaggi in acciaio sta provvedendo ad eliminare progressivamente la verniciatura a base PVC utilizzando materiali vernicianti diversi che facilitano le attività di riciclo.
Un discorso a parte va fatto, invece, per componenti realizzati anch’essi in acciaio; in questo caso, la separabilità è, all’opposto di quanto indicato precedentemente, sconsigliata ed è preferibile progettare i componenti affinché rimangano solidali con il corpo principale dell’imballaggio (si vedano, ad esempio, le soluzioni di imballaggio open top in cui le linguette rimangono unite al resto della struttura). Durante il processo di riciclo, anche se gli impianti di trattamento sono dotati di strumenti che individuano e isolano i rottami di piccole dimensioni, elementi di volume ridotto rischiano, infatti, di disperdersi e di non essere recuperati.
Focus: Etichette
Un'altra considerazione va fatta poi sulle etichette, che spesso rimangono attaccate al corpo principale dell'imballaggio a causa dell'elevata quantità di adesivi impiegati. Sebbene gli elementi in materiale cellulosico non siano problematici ai fini delle attività di riciclo, è raccomandabile ridurre i punti di colla per facilitare la rimozione delle etichette, eventualmente agevolata dall'aggiunta di perforazioni che ne consentano un più rapido strappo. Inoltre, può essere utile aggiungere suggerimenti sulla confezione che ricordino al consumatore di rimuovere l’etichetta e smaltirla nella frazione di materiale pertinente.
In sintesi, a parità di prestazioni, è preferibile:
- ridurre il numero di componenti accessori e adottare soluzioni monomateriale;
- evitare o comunque ridurre al minimo l’utilizzo di componenti rigidi in plastica;
- agevolare la completa separazione di componenti in materiali diversi dall’acciaio;
- evitare la dispersione di componenti in acciaio di dimensioni ridotte (per esempio, linguette e coperchi usa e getta), facendo sì che si mantengano uniti all’imballaggio e non si separino;
- nel caso di sistemi di chiusura in acciaio applicati a imballaggi in altri materiali (per esempio, barattoli e bottiglie in vetro), ottimizzare la forma e ridurre la quantità di materiale utilizzato per minimizzare le possibili perdite se questi elementi non vengono riciclati;
- rendere le etichette facilmente removibili mediante riduzione di punti di colla e l’aggiunta di perforazioni o altri sistemi per un più facile strappo;
- informare e guidare il consumatore alla corretta separazione dei componenti accessori e al loro corretto smaltimento nella raccolta differenziata.
Residui e svuotamento
Progettare gli imballaggi in un'ottica di riduzione dell'impatto ambientale e, ancor più, di facilitazione delle attività di riciclo presuppone una valutazione complessiva della struttura del packaging, non solo in termini di quantità assoluta di materiale utilizzato, di spessori o numero di componenti, ma anche in relazione al prodotto che contiene e al rapporto tra contenuto e contenitore. Tale rapporto riguarda, come già visto, la protezione e la conservazione del prodotto, la compatibilità fisico-chimica con esso e l'adeguatezza del volume e della quantità dei materiali di imballaggio rispetto alla quantità di contenuto, per evitare, per esempio, di incorrere nel cosiddetto over-packaging (eccesso di imballaggio).
Tuttavia, la relazione contenuto-contenitore riguarda anche un altro fattore, ovvero la facilità con cui un packaging consente di essere svuotato dall'utente finale, evitando la generazione di residui al suo interno che, oltre a costituire uno spreco di prodotto, in alcuni casi possono pregiudicare un risultato ottimale delle attività di riciclo. In questo senso, è importante notare come la Direttiva 94/62/CE e la norma UNI EN 13430:2005 mettano in evidenza proprio l'importanza dello svuotamento completo degli imballaggi, al fine di minimizzare eventuali sostanze rilasciate o residui durante il processo di riciclo, non solo nel caso degli imballaggi identificati come pericolosi, ma anche per quelli destinati a un uso domestico.
Va segnalato che, in linea generale, la presenza di residui non rappresenta un limite significativo alle operazioni di riciclo dei packaging in acciaio: qualora gli imballaggi presentino minime quantità di prodotto al momento del conferimento, questi resti vengono rimossi durante le fasi di selezione e pretrattamento dei rifiuti, per poi dissolversi completamente durante il riciclo vero e proprio del materiale. Tuttavia, per ottimizzare il più possibile il processo di riciclo e migliorarne il risultato, è comunque raccomandabile adottare in fase di progettazione accorgimenti specifici per favorire lo svuotamento completo del packaging, soprattutto in presenza di un contenuto più denso e difficile da rimuovere.
Particolare attenzione va poi prestata agli imballaggi che vengono conferiti sigillati e pieni, ad esempio nel caso di alimenti scaduti. Attraverso un'efficace comunicazione, è possibile sensibilizzare l’utente finale e incoraggiare lo svuotamento completo del packaging prima di gettarlo nella raccolta differenziata. Inoltre, scelte progettuali mirate possono facilitare la rimozione di contenuto dalla confezione, come ad esempio un'apertura più ampia e forme prive di punti di accumulo dove il prodotto è più difficile da rimuovere.
Focus: bombolette aerosol
Rispetto allo svuotamento completo delle confezioni, si sottolinea l'importanza cruciale di non lasciare residui all’interno delle bombolette spray, poiché durante il processo di riciclo si possono generare problemi di sicurezza per possibili incendi e scoppi. Per questi motivi, sebbene le bombolette spray siano di fatto facilmente riciclabili in termini di materiale, richiedono comunque delle accortezze specifiche, a seconda del tipo di propellente che contengono.
I propellenti comunemente utilizzati possono essere di due tipi: a base di idrocarburi, come il propano, o non a base di idrocarburi, come l'anidride carbonica o il protossido di azoto. Sono i propellenti a base di idrocarburi che possono causare problemi di sicurezza, ad esempio, durante la compattazione dei materiali negli impianti di selezione e recupero, quando lo sfregamento del materiale può generare scintille e provocare combustioni per la presenza del propellente.
È essenziale, quindi, comunicare all’utente finale l’importanza di svuotare completamente le bombolette prima di conferirle nell'apposita raccolta differenziata, l'operazione di svuotamento della bomboletta può essere possibile tramite l’erogatore presente nella confezione oppure integrando in fase progettuale delle soluzioni che facilitino lo sfiatamento del packaging a fine vita.
Oltre al problema dei residui, un altro punto di attenzione per il riciclo delle bombolette aerosol è la presenza di componenti in plastica. Anche in questo caso è fondamentale una comunicazione efficace all'utente finale sulla corretta separazione dei componenti prima dello smaltimento nella raccolta differenziata, per facilitare il processo di riciclo.
In sintesi, a parità di prestazioni, è preferibile:
- optare per strutture che favoriscano il completo svuotamento del packaging, adottando soluzioni specifiche in base al tipo di contenuto (liquido, viscoso, solido, in polvere, gassoso), per esempio prevedendo imboccature ampie e forme che non presentino zone in cui il prodotto si accumula senza poter essere rimosso;
- comunicare all’utente l’importanza di svuotare completamente l’imballaggio da eventuali residui di contenuto, prima di conferirlo nella raccolta differenziata. In particolare, nel caso di confezioni ancora sigillate e piene segnalare di conferirle ai Centri di Raccolta Comunali.
Trattamenti superficiali
I trattamenti superficiali sono applicazioni che mirano a migliorare le caratteristiche funzionali o le qualità estetiche degli imballaggi in acciaio. I vantaggi di questi trattamenti sono molteplici: da un punto di vista funzionale, consentono di rendere l'imballaggio adatto a contenere sostanze chimiche particolarmente aggressive; permettono di soddisfare specifici requisiti igienico-sanitari e di idoneità al contatto con alcuni alimenti; oppure, contribuiscono a rafforzare la proprietà barriera del materiale per preservare e prolungare la shelf-life dei prodotti.
Tuttavia, dato l'impatto che alcune applicazioni possono avere sulle attività di riciclo, è sempre consigliabile limitare i trattamenti, soprattutto quando non sono strettamente necessari. Quando invece non se ne può fare a meno perché i trattamenti superficiali forniscono all'imballaggio prestazioni essenziali, è importante prendere le dovute precauzioni per non ostacolare il riciclo.
Focus: Verniciature
Nel caso di lacche e vernici, quando possibile, è raccomandabile utilizzare processi di verniciatura a basso impatto (come, per esempio, la verniciatura a UV/LED). È inoltre preferibile utilizzare lacche a base d'acqua e vernici a ridotto contenuto di composti organici volatili (VOC), che non comportano impatti significativi durante il processo di riciclo.
In sintesi, a parità di prestazioni, è preferibile:
- utilizzare trattamenti superficiali solo se strettamente necessari per garantire una proprietà che non può essere ottenuta con altre soluzioni;
- privilegiare processi di verniciatura a basso impatto;
- quando possibile, impiegare lacche a base d’acqua e vernici a basso contenuto di COV.
Comunicazione al consumatore
Per garantire un risultato di riciclo di qualità, oltre ad adottare accorgimenti in fase di progettazione per rendere gli imballaggi più facilmente riciclabili, è fondamentale coinvolgere gli utenti finali per sensibilizzarli a una corretta raccolta differenziata dei packaging in acciaio. Nella fase di raccolta, infatti, mentre il settore industriale genera scarti omogenei in termini di qualità, il flusso cittadino vede l'accumulo di diverse tipologie di rifiuti, per questo è essenziale che questi vengano differenziati opportunamente a monte.
È fondamentale quindi che gli utenti finali siano consapevoli delle buone pratiche legate al corretto conferimento dei contenitori con cui vengono a contatto. Questa consapevolezza è essenziale per garantire l’ottimizzazione dei processi di riciclo e chi progetta, oltre a intervenire sull'imballaggio nella sua dimensione di oggetto d'uso, deve lavorare anche su quella di “mezzo di comunicazione” capace di orientare i comportamenti delle persone.
Il contributo in questo senso è ancora più importante quando il progettista riesce a portare l'utente a compiere azioni virtuose in modo quasi automatico, senza la necessità di una formazione mirata o con una quantità di informazioni pregresse ridotte al minimo. È per questi motivi che, dalle prime fasi del processo progettuale, è importante definire le modalità comunicative più idonee per far sì che l’imballaggio venga conferito nella raccolta differenziata nel modo corretto. È essenziale che il cittadino sappia riconoscere ciò che effettivamente è un imballaggio da ciò che non lo è, e cosa fare con i diversi rifiuti.
L’11 settembre 2020 è stato pubblicato in Gazzetta Ufficiale il decreto legislativo 3 settembre 2020, n. 116, che recepisce la direttiva (UE) 2018/851 sui rifiuti, e la direttiva (UE) 2018/852 relativa agli imballaggi e ai rifiuti di imballaggio. Il decreto ha introdotto l’obbligo di etichettatura ambientale per tutti gli imballaggi immessi al consumo in Italia a partire dal 1° gennaio 2023. Il testo di legge indica esplicitamente che su tutti gli imballaggi (B2B e B2C) siano riportate le identificazioni dei materiali mediante la decisione 129/97/CE. Gli imballaggi destinati ai consumatori finali devono inoltre prevedere le indicazioni sul corretto conferimento in raccolta. CONAI suggerisce di indicare chiaramente la famiglia di materiale prevalente dell’imballaggio, che nel caso di acciaio e alluminio può anche essere identificata come “metalli” in quanto la raccolta è unica e generalmente indicata in questo modo dai gestori delle raccolte differenziate domestiche.
In generale, le informazioni inerenti all’etichettatura ambientale e al conferimento di un imballaggio/rifiuto nella raccolta differenziata devono saper rispondere a tre domande principali:
- che cosa è? cioè se l'imballaggio può essere ricondotto a un tipo specifico di materiale (Codifica alfanumerica da Decisione 129/97/CE e famiglia di materiale);
- dove deve essere conferito? cioè se può essere conferito nella raccolta differenziata e in quale cassonetto (Informazioni sulla raccolta);
- come va trattato? cioè come bisogna intervenire sul rifiuto prima di conferirlo nella raccolta differenziata (le indicazioni al consumatore per supportarlo in una raccolta differenziata di qualità).
Utilizzare messaggi semplici in etichetta e forme comunicative di immediata comprensione contribuisce a indirizzare correttamente gli imballaggi nella raccolta differenziata. Facilitare, per esempio, il sistema di riconoscimento visivo dei materiali non soltanto attraverso i codici identificativi obbligatori (per esempio, “FE 40” per gli imballaggi in acciaio) ma anche attraverso le informazioni aggiuntive volontarie si è dimostrato essere particolarmente efficace nella fase di raccolta differenziata. Inoltre, l'integrazione dell'etichettatura ambientale obbligatoria, come prevista dal D.M. 360 del 28 settembre 2022, con le informazioni ai consumatori su come smaltire correttamente gli imballaggi ha certamente contribuito a rendere il processo di riciclo più agevole. CONAI, a tal proposito, ha reso disponibile il documento “Linee guida per una etichettatura ambientale volontaria per gli imballaggi” utile alle imprese interessate ad apporre volontariamente dichiarazioni o etichette ambientali aggiuntive sugli imballaggi.
Per quanto riguarda gli altri messaggi che è consigliabile aggiungere sulle confezioni, come visto in precedenza, è possibile fornire istruzioni sulla separazione dei componenti, semplificando, per esempio, il riconoscimento e lo smontaggio di parti di materiali diversi (per esempio, tappi o dispenser in plastica), oppure la compattazione e la riduzione del volume delle confezioni.
È importante, infine, che siano facilmente identificabili gli imballaggi pericolosi e che sia chiaro come questi debbano essere gestiti: è infatti necessario comunicare tramite etichettatura che tale contenuto può generare dei rischi durante le fasi del riciclo, per questo è necessario conferire l’imballaggio vuoto e rimuovere in maniera efficace il residuo limitando quanto più possibile lo sgocciolamento delle sostanze pericolose.
In sintesi, è consigliabile:
- invitare l’utente a porre attenzione al fine vita dell’imballaggio e al ruolo che ricopre rispetto al suo corretto riciclo;
- veicolare messaggi che portino l’utente a compiere buone pratiche in fase di uso e di conferimento;
- fornire all’utente informazioni utili e chiare circa i materiali di cui è costituito l’imballaggio, nel rispetto della normativa di riferimento;
- fornire indicazioni specifiche sulla gestione dell’imballaggio in fase di conferimento, dalla separazione dei componenti allo svuotamento del packaging, fino alla manipolazione degli imballaggi pericolosi.
Check-list per progettisti e aziende
> Checklist Informativa
> Checklist di valutazione
Glossario
BIODEGRADAZIONE
La biodegradazione è un processo termochimico che avviene entro un determinato lasso temporale e in presenza di specifiche condizioni ambientali. Durante la biodegradazione i materiali/prodotti sono convertiti in biomassa, acqua e anidride carbonica.
FONTE: Greene, J.P. (2014). Sustainable Plastics: Environmental Assessments of Biobased, Biodegradable, and Recycled Plastics. (1st Ed). John Wiley & Sons.
COKE
Residuo della distillazione del carbon fossile. Si ottiene per riscaldamento dei litantraci senza contatto dell’aria. Può costituire un prodotto secondario rispetto al gas di distillazione o il prodotto principale quando impiegato negli altiforni e in fonderia (coke metallurgico); nei due casi i carboni di partenza sono diversi (grassi, rispettivamente a lunga e a corta fiamma). Il processo di trasformazione del fossile in coke avviene in storte di distillazione, camere alte e profonde ma strette, nelle quali si carica il carbone; a contatto delle pareti calde della storta di distillazione, dopo l’eliminazione dei gas occlusi e l’evaporazione dell’acqua, si ha l’eliminazione di una parte delle sostanze volatili e la formazione di una massa plastica semifusa che, sopra 450 °C, si consolida dando il cosiddetto semicoke. A temperature ancora superiori, 900-1100 °C, si ha l’ulteriore eliminazione di sostanze volatili mentre la massa residua forma il coke propriamente detto. In seguito al progressivo riscaldamento della carica, si nota una continua variazione nella composizione del gas risultante. Dapprima esso è ricco di idrocarburi superiori (alifatici e aromatici), come anche metano, e aliquote di CO e CO₂ che si originano per reazione tra vapor d’acqua (proveniente dalla disidratazione della carica) e carbone rovente. Successivamente si osserva un progressivo aumento del tenore di idrogeno (nella fase finale si giunge a circa l’80%): questo gas deriva dalla decomposizione termica delle sostanze organiche presenti; anche il metano, sopra 800 °C, si piroscinde dando idrogeno e carbonio, il quale cementa il coke, che risulta pertanto tanto più compatto quanto più alta è la temperatura di distillazione. Il coke metallurgico è più compatto, duro e resistente allo schiacciamento: ai fini del suo impiego negli altiforni ha grande importanza la quantità (max 9%) e la natura chimica delle ceneri cui dà origine per completa combustione.
FONTE: Enciclopedia Treccani.
COMPOSTI ORGANICI VOLATILI (COV)
In base al comma 11, art.268 del D.Lgs. 152/2006, vengono definiti COV qualsiasi composto organico che abbia a 293,15 K (20 °C) una pressione di vapore di 0,01 KPa superiore. Varie sono le sorgenti di inquinamento di Composti Organici Volatili (COV) nell'aria degli ambienti indoor: gli “occupanti” attraverso la respirazione e la superficie corporea, i prodotti cosmetici o deodoranti, i dispositivi di riscaldamento, i materiali di pulizia e prodotti vari (es. colle, adesivi, solventi, vernici), abiti trattati recentemente in lavanderie, il fumo di sigaretta e strumenti di lavoro, quali stampanti e fotocopiatrici. I COV possono essere causa di una vasta gamma di effetti che vanno dal disagio sensoriale fino a gravi alterazioni dello stato di salute; ad alte concentrazioni negli ambienti interni possono causare effetti a carico di numerosi organi o apparati, in particolare a carico del sistema nervoso centrale. Alcuni di essi sono riconosciuti cancerogeni per l'uomo (benzene) o per l'animale (tetracloruro di carbonio, cloroformio, tricloroetilene, tetracloroetilene).
FONTE: Ministero della Salute, Composti Organici Volatili, www.salute.gov.it.
CORRODIBILITÀ
Grado di resistenza di una sostanza metallica o di un materiale metallico alla corrosione, ossia al deperimento a contatto con reagenti chimici (corrosione chimica o in ambiente secco) o per effetto di fenomeni elettrochimici (corrosione elettrochimica o in ambiente umido).
FONTE: Bucchetti, V., Ciravegna, E. (2009). Le parole del packaging: Glossario Ragionato per il sistema-imballaggio. Dativo.
DUREZZA
Grado di deformabilità plastica di un materiale. È definita come la resistenza alla deformazione permanente. Le prove di durezza determinano la resistenza offerta da un materiale a lasciarsi penetrare da un altro (penetratore). Esistono diverse scale per misurare la durezza, le più usate sono: Brinell; Vickers; Rockwell; Mohs.
FONTE: Bucchetti, V., Ciravegna, E. (2009). Le parole del packaging: Glossario Ragionato per il sistema-imballaggio. Dativo.
ECONOMIA CIRCOLARE
Un'economia industriale riparativa e rigenerativa che mira a mantenere i prodotti, i componenti e i materiali sempre al loro massimo livello di utilità e valore, distinguendo i cicli tecnici da quelli biologici.
FONTE: Ellen MacArthur Foundation.
IDROCARBURO
In chimica, nome generico di tutti i composti organici formati unicamente di carbonio e idrogeno. Si presentano come sostanze gassose, liquide, solide, generalmente incolori, insolubili in acqua, che vengono usate come solventi, come carburanti, come combustibili e come materie prime per la sintesi di numerosi prodotti industriali (tra cui gomme sintetiche, sostanze plastiche, prodotti farmaceutici e concimi).
FONTE: Enciclopedia Treccani.
IMBALLAGGI INTELLIGENTI
Chiamati anche con l'espressione anglosassone intelligent packaging, sono imballaggi funzionali progettati per monitorare lo stato di conservazione dell’alimento confezionato attraverso il rilascio/assorbimento di sostanze.
FONTE: Bucchetti, V., Ciravegna, E. (2009). Le parole del packaging: Glossario Ragionato per il sistema-imballaggio. Dativo.
IMBALLAGGI MULTIMATERIALE
Si intende l'imballaggio costituito da più componenti autonome in materiali diversi. A differenza dell’imballaggio composito, in questo caso i diversi materiali che costituiscono l’imballaggio possono essere separati. Ad esempio, sono considerati imballaggi multimateriali: scatola di cioccolatini (carta per la scatola, plastica per il contenitore sagomato all’interno), sacchetto di caramelle (plastica per il sacchetto, carta per le singole caramelle), barattolo di caffè (alluminio per il barattolo, plastica per il coperchio), ecc.
FONTE: CONAI (2020). Guida all’adesione e all’applicazione del Contributo Ambientale (Volume 1).
IMBALLAGGIO ATTIVO
Un imballaggio viene definito attivo quando sono previste una o più forme di interazione con il proprio contenuto, comunemente per migliorare le prestazioni del contenitore e compensare una carenza. Il componente attivo può far parte del materiale di imballaggio o essere un inserto o un componente all'interno della confezione. La lattina in banda stagnata, per esempio, fornisce uno strato sacrificale di stagno che protegge gli alimenti dall'accumulo di sali di ferro cataliticamente attivi.
FONTE: Kit L. Yam (2009). Encyclopedia of Packaging Technology. John Wiley & Sons, Inc.
IMBALLAGGIO FLESSIBILE
Struttura realizzata in materiale flessibile o facilmente piegabile la cui forma, dopo il riempimento e la chiusura, può cambiare.
FONTE: Bucchetti, V., Ciravegna, E. (2009). Le parole del packaging: Glossario Ragionato per il sistema-imballaggio. Dativo.
LAMINAZIONE
Processo meccanico che avviene mediante cilindri contrapposti che, ruotando su se stessi, imprimono nel materiale la forma e lo spessore desiderati. Il termine laminazione indica anche l'operazione secondo cui viene coperto un foglio stampato con un sottile strato protettivo in materiale plastico o metallico detto laminato.
FONTE: Bucchetti, V., Ciravegna, E. (2009). Le parole del packaging: Glossario Ragionato per il sistema-imballaggio. Dativo.
LEGA METALLICA
È una miscela di due o più elementi di cui almeno uno è un metallo, e il cui materiale risultante ha proprietà metalliche differenti da quelle dei relativi componenti.
FONTE: Spigarelli, S. (2012). Metallurgia meccanica. Esculapio.
MATERIALE INERTE
Materiale che non reagisce o reagisce molto poco con altri materiali o sostanze.
FONTE: Callister, W., Rethwisch, D. (2019). Scienza ed Ingegneria dei Materiali. Edises.
MATERIA PRIMA SECONDA
Insieme dei rifiuti che cessano di essere tali qualora siano sottoposti a un’operazione di recupero, incluso il riciclaggio, e soddisfino criteri specifici.
FONTE: Decreto Legislativo 205/10, Articolo 184-ter (3 dicembre 2010).
MULINO
Dispositivo che utilizza una forza motrice per applicare una pressione o un attrito su un materiale, causandone la rottura.
FONTE: Smith, W., Hashemi, J. (2016). Scienza e tecnologia dei materiali. McGraw-Hill.
OSSIDAZIONE
Reazione chimica nella quale una molecola perde uno o più elettroni cedendoli a un’altra specie. A seguito del processo, uno o più atomi della prima specie aumentano il loro grado di ossidazione (si ossidano), mentre uno o più atomi della seconda lo diminuiscono (si riducono).
FONTE: Enciclopedia della Scienza e della Tecnica Treccani.
PERFORAZIONE
Operazione che produce un foro o una serie di fori attraverso una materia compatta.
FONTE: Enciclopedia Treccani.
PORTALE RADIOMETRICO
Sistema di controllo che utilizza la rilevazione di radiazioni ionizzanti per identificare e monitorare la presenza di materiali radioattivi.
FONTE: Federacciai.
PREVENZIONE
Riduzione, in particolare attraverso lo sviluppo di prodotti e di tecnologie non inquinanti, della quantità e della nocività per l’ambiente sia delle materie e delle sostanze utilizzate negli imballaggi e nei rifiuti di imballaggio, sia degli imballaggi e rifiuti di imballaggio nella fase del processo di produzione, nonché in quella della commercializzazione, della distribuzione, dell’utilizzazione e della gestione post-consumo.
FONTE: Direttiva 2008/98/CE, art. 3, comma 12.
PROLER
Rottami ferrosi macinati e ridotti in piccola pezzatura.
FONTE: RICREA. RGPS 2019.
RACCOLTA DIFFERENZIATA
È la raccolta idonea, secondo criteri di economicità, efficacia, trasparenza ed efficienza, a raggruppare i rifiuti urbani in frazioni merceologiche omogenee, al momento della raccolta o, per la frazione organica umida, anche al momento del trattamento, nonché a raggruppare i rifiuti di imballaggio separatamente dagli altri rifiuti urbani, a condizione che tutti i rifiuti sopra indicati siano effettivamente destinati al recupero.
FONTE: Decreto Legislativo 152/06, Articolo 183, Comma 1 Lettera f (3 aprile 2006).
RACCOLTA MULTIMATERIALE
Le diverse tipologie di raccolte multimateriali effettuabili possono essere suddivise sulla base dei materiali che si vogliono raccogliere distinguendo, a grandi linee, le seguenti categorie:
- raccolta multimateriale “pesante”: riguarda una quota piuttosto limitata dei rifiuti (bottiglie e flaconi in vetro e plastica, lattine metalliche), che può indicativamente rappresentare il 15-20% dei rifiuti complessivamente prodotti;
- raccolta multimateriale “leggera”: comprende le frazioni secche riciclabili del rifiuto, escluso il vetro; riguarda pertanto materiali quali carta, plastica e metalli, arrivando a interessare il 30-40% dei rifiuti totali.
FONTE: Ispra, Definizione di standard tecnici nei servizi di igiene urbana.
RECUPERO
Qualsiasi operazione il cui principale risultato sia di permettere ai rifiuti di svolgere un ruolo utile sostituendo altri materiali che sarebbero stati altrimenti utilizzati per assolvere una particolare funzione o di prepararli ad assolvere tale funzione, all’interno dell’impianto o nell’economia in generale.
FONTE: Direttiva 2008/98/CE, art. 3, comma 15.
RECUPERO ENERGETICO (TERMOVALORIZZAZIONE)
Secondo quanto disposto dall’art. 218, comma 1, lettera n) del D.Lgs. 152/06, il recupero energetico dei rifiuti di imballaggio si ha quando tali rifiuti di imballaggio combustibili vengono utilizzati per produrre energia mediante termovalorizzazione (con o senza altre tipologie di rifiuto) con recupero di calore.
FONTE: CONAI (2020). Guida all’adesione e all’applicazione del Contributo Ambientale (Volume 1).
RESISTENZA MECCANICA
Capacità di un materiale di resistere all'azione di forze esterne che possono deformarlo o romperlo.
FONTE: Smith, W., Hashemi, J. (2016). Scienza e tecnologia dei materiali. McGraw-Hill.
RICICLAGGIO
Qualsiasi operazione di recupero attraverso cui i materiali di rifiuto sono ritrattati per ottenere prodotti, materiali o sostanze da utilizzare per la loro funzione originaria o per altri fini. Include il ritrattamento di materiale organico ma non il recupero di energia né il ritrattamento per ottenere materiali da utilizzare quali combustibili o in operazioni di riempimento.
FONTE: Direttiva 2008/98/CE, Articolo 3, comma 17 (19 novembre 2008). Disponibile presso EUR-Lex.
RIFIUTO
Qualsiasi sostanza od oggetto di cui il detentore si disfi o abbia l’intenzione o l’obbligo di disfarsi.
FONTE: Direttiva 2008/98/CE, art. 3, comma 1.
RIUTILIZZO DEGLI IMBALLAGGI
Operazione attraverso il quale il prodotto da imballaggio, che per sua struttura può essere utilizzato più volte, viene riempito o reimpiegato per un uso identico a quello per il quale è stato concepito. In questo caso non si ha produzione di rifiuti di imballaggio, venendo a mancare nel detentore la volontà di “disfarsi” dell’imballaggio.
FONTE: Consorzio RICREA. Glossario.
SALDATURA
Procedimento che permette il collegamento permanente di parti solide tra loro e che realizza la continuità del materiale ove essa venga applicata. La saldatura nella sua accezione più comune presuppone l'apporto di calore localizzato tale da permettere la fusione del materiale: la qualità della saldatura a caldo, o termosaldatura, è determinata dalle sostanze utilizzate nel processo, dal tempo, dalla temperatura e dalla pressione. La saldatura a ultrasuoni è un metodo di sigillatura a caldo realizzata tramite l'applicazione di frequenze ultrasoniche (da 20 a 40 kHz) ai materiali da unire; la vibrazione sulle interfacce genera un calore sufficientemente localizzato da ammorbidire e fondere i materiali termoplastici. La saldatura a coesione o saldatura a freddo è invece prodotta da un adesivo e richiede una pressione di contatto per legarsi.
FONTE: Bucchetti, V., Ciravegna, E. (2009). Le parole del packaging: Glossario Ragionato per il sistema-imballaggio. Dativo.
SHELF LIFE
La shelf life o “vita di scaffale” di un prodotto è il tempo stimato della sua durata, in altre parole il periodo durante il quale la qualità del prodotto rimane inalterata.
FONTE: Bucchetti, V., Ciravegna, E. (2009). Le parole del packaging: Glossario Ragionato per il sistema-imballaggio. Dativo.
SIDERURGIA
È l’insieme delle tecniche che hanno per scopo la produzione e la prima lavorazione del ferro, della ghisa, dell’acciaio e delle ferroleghe, fino alla produzione di semilavorati quali lingotti, billette, lamiere ecc. Comprende la siderurgia estrattiva, che si occupa della produzione della ghisa di prima fusione dai minerali di ferro e la siderurgia tecnologica, che si occupa della fabbricazione dei vari tipi di acciai e di ghisa.
FONTE: Enciclopedia Treccani.
TENACITÀ
È una misura dell’energia che un provino può assorbire prima di rompersi. Si ricava dal rapporto tra l'energia necessaria alla rottura (che corrisponde all'area sottesa alla curva) e la superficie del provino.
FONTE: Piergiovanni, L., & Limbo, S. (2010). Food packaging: Materiali, tecnologie e soluzioni, Milano, Springer-Verlag.
TRATTAMENTI SUPERFICIALI
Processo come coating, rivestimento o laccatura, attraverso il quale uno strato sottile di materiale fluido o fuso viene applicato sulla superficie di un substrato, che nella maggior parte dei casi è un film plastico, ma può essere anche un foglio di carta, una scatola metallica o un vetro.
FONTE: Piergiovanni L., Limbo S., (2010). Food packaging: Materiali, tecnologie e soluzioni, Milano, Springer-Verlag.
TRATTAMENTO MECCANICO BIOLOGICO
Impianti che effettuano un trattamento meccanico del rifiuto urbano residuo (RUR), eventualmente combinato con un trattamento biologico di bioessiccazione o biostabilizzazione.
FONTE: Biganzoli L., Grosso M., (2015). Il ruolo del Trattamento Meccanico Biologico nel panorama di gestione dei rifiuti solidi urbani in Italia. Centro studi Mater.
VAGLIATURA
Far passare attraverso un vaglio una massa incoerente, granulare o frammentaria, sia per separare la parte utile da scorie, mondiglia, corpi estranei, sia per dividere gli elementi di una data dimensione da altri di dimensione maggiore.
FONTE: Enciclopedia della Scienza e della Tecnica Treccani.
Normativa di riferimento
Comunicazione della Commissione al Parlamento europeo, al consiglio, al comitato economico e sociale europeo e al comitato delle regioni su un quadro di monitoraggio riveduto per l'economia circolare, COM2023/206.
Decisione 97/129/CE: Decisione della Commissione del 28 gennaio 1997 che istituisce un sistema di identificazione per i materiali di imballaggio ai sensi della direttiva 94/62/CE del Parlamento europeo e del Consiglio sugli imballaggi e i rifiuti di imballaggio.
Decreto Legislativo del 3 aprile 2006, n. 152, Norme in materia ambientale.
Decreto Legislativo del 3 settembre 2020, n. 116, Attuazione della direttiva (UE) 2018/851 che modifica la direttiva 2008/98/CE relativa ai rifiuti e attuazione della direttiva (UE) 2018/852 che modifica la direttiva 1994/62/CE sugli imballaggi e i rifiuti di imballaggio.
Decreto Ministeriale del 28 settembre 2022, n.360, che adotta le Linee Guida sull’etichettatura ambientale ai sensi dell’art. 219, comma 5, del decreto legislativo 3 aprile 2006, n. 152, per il corretto adempimento degli obblighi di etichettatura degli imballaggi da parte dei soggetti responsabili.
Direttiva (EU) 94/62/CE del Parlamento europeo e del Consiglio, del 20 dicembre 1994, sugli imballaggi e i rifiuti di imballaggio.
Direttiva (EU) 2004/12/CE del Parlamento europeo e del Consiglio, dell'11 febbraio 2004, che modifica la direttiva 94/62/CE sugli imballaggi e i rifiuti di imballaggio – Dichiarazione del Consiglio, della Commissione e del Parlamento europeo.
Direttiva (EU) 2008/98/CE del Parlamento Europeo e del Consiglio del 19 novembre 2008 relativa ai rifiuti e che abroga alcune direttive.
Direttiva (UE) 2018/852 del Parlamento europeo e del Consiglio, del 30 maggio 2018, che modifica la direttiva 94/62/CE sugli imballaggi e i rifiuti di imballaggio.
Bibliografia e sitografia
BIBLIOGRAFIA
Berger, K. R. (2002). A brief history of packaging. University of Florida Cooperative Extension Service, Institute of Food and Agricultural Sciences, EDIS.
Bucchetti, V. (2005). Packaging design. Storia, linguaggi, progetto. Poli.Design. FrancoAngeli.
Bucchetti, V., Ciravegna, E. (2009). Le parole del packaging: Glossario Ragionato per il sistema-imballaggio. Dativo.
Celaschi, F. (2008). Design mediatore tra bisogni. In Germak, C. (Ed.), Uomo al centro del progetto Design per un nuovo umanesimo (pp. 40–52). Allemandi.
CONAI. (2014). Etichetta per il cittadino: Vademecum per una etichetta volontaria ambientale che guidi il cittadino alla raccolta differenziata degli imballaggi.
Maris, E., Froelich, D., Aoussat, A., & Naffrechoux, E. (2014). From recycling to eco-design. In Handbook of recycling (pp. 421-427). Elsevier.
McDonough, W., & Braungart, M. (2010). Cradle to cradle: Remaking the way we make things. North Point Press.
Parlamento Europeo (2023). Economia circolare: in che modo l’UE intende realizzarla entro il 2050? https://www.europarl.europa.eu/news/it/headlines/society/20210128STO96607/economia-circolare-in-che-modo-l-ue-intende-realizzarla-entro-il-2050
Pellizzari, A., & Genovesi, E. (2021). Neomateriali 2.0 nell’economia circolare. Ambiente.
Piergiovanni, L., & Limbo, S. (2010). Food packaging: Materiali, tecnologie e soluzioni. Springer Science & Business Media.
RICREA. (2022). Green Economy Report.
RICREA. (2023). Relazione sulla gestione 2022 Bilancio e programma specifico di prevenzione.
Rigamonti, L., Grosso, M., Biganzoli, L., Tua, C. (2018). Mappatura delle pratiche di riutilizzo degli imballaggi in Italia: Valutazione LCA della pratica di riutilizzo dei fusti in acciaio per prodotti chimici e petrolchimici. CONAI.
Wang, P. et al. (2021). Efficiency stagnation in global steel production urges joint supply- and demand-side mitigation Efforts. Nature Communication.
SITOGRAFIA
Consorzio RICREA.
https://www.consorzioricrea.org/
Etichetta CONAI.
https://www.etichetta-conai.com/documenti/linee-guida-per-una-etichettatura-ambientale-volontaria/
https://www.etichetta-conai.com/faqs/si-puo-usare-la-parola-metalli-al-posto-di-acciaio-e-alluminio/
Metal Packaging Europe.
https://metalpackagingeurope.org/
Pensare Futuro CONAI.
https://www.conai.org/prevenzione-eco-design/pensare-futuro/
Progettare riciclo.
https://www.progettarericiclo.com/
Recycles Forever.
https://www.